Laatutaulu: kehitysvaiheet I-II – teoriasta käytäntöön: Osa 2
Laatutaulu on julkinen isokokoinen taulupari, johon on koottuna valmistusprosessin aikana päivittäin, viikoittain tai kuukausittain havaitut luokitellut poikkeamat. Poikkeamat analysoidaan, diagnostisoidaan ja jaetaan tilastollisesti ohjausrajojen (C-raja) avulla erityissyihin ja satunnaissyihin. Erityissyyperusteisten poikkeamien (ilmenemismuotojen) juurisyyt selvitetään vastuuhenkilön toimesta erityissyytaululla ja tehdään korjaus, ohjaus tai parannustoimenpide. Toimenpide merkitään taululle ja valmistumishetki. Kaikki tämä julkisesti kaikkien koko henkilöstön nähden.

Laatutaulumenetelmä on poikkeamien (virheiden, vikojen ja kaikkien hukkien) ennaltaehkäisymenetelmä, joka perustuu tri Walter A. Shewhartin vuonna 1924 keksimään ja tri W. Edwards Demingin kehittämään laatuteoriaan (1, 2). Tämä teoria mahdollisti ennaltaehkäisyn, jota myös kutsutaan jatkuvaksi parantamiseksi ja on osa PDSA-laatuympyrää. PDSA-ympyrä/jakso (laatuympyrä) on tarkoitettu Demingin mukaan satunnaissyyperusteisille ongelmille. Sitä käytetään myös Leanin ja juurisyyanalyysien yhteydessä ja monessa muussakin paikassa (erityissyyperusteinen ongelma) ilman, että on selvitetty prosessin tila. Koe(suunnittelu), jota PDSA kuvaa, vaatii stabiilin ja ennustettavan olosuhteen.
Laatuteorian (=SPC) keskeinen sanoma on, että tulevaisuudessa, siis huomenna, olevat poikkeamien syyt voidaan luokitella menneiden ja tämän päivän tapahtumien perusteella, erityissyyperusteisiksi ja satunnaissyyperusteiseksi. Tämä ratkaisee, kuinka poikkeamaa, virhettä, vikaa tai kaikkia hukkia, on käsiteltävä. Yleissääntö on, että vain erityissyyperusteisen ongelman syy voidaan löytää (nimetä syy, assignable cause) ja satunnaisperusteisen ongelman syytä EI VOI löytää (ei voi nimetä syytä, satunnaiset syyt, common causes), mutta voidaan kokeellisesti löytää vaikuttavia kausaalitekijöitä. Tähän kokeelliseen tutkimukseen liittyy PDSA. Systeemissä juurisyyn olemassaolo on kyseenalainen. Mieti lottoarvontaa (tulosta). Löytyykö juurisyy? Mieti, jokin prosessi. Löytyykö juurisyy? Enpä usko!
Tri W. E. Deming toteaa kirjassaan (2) Shewhartin jaksosta: ”PDSA-jakso. Tämä on virtauskaavio oppimiseen ja tuotteen tai prosessin parantamiseen.”
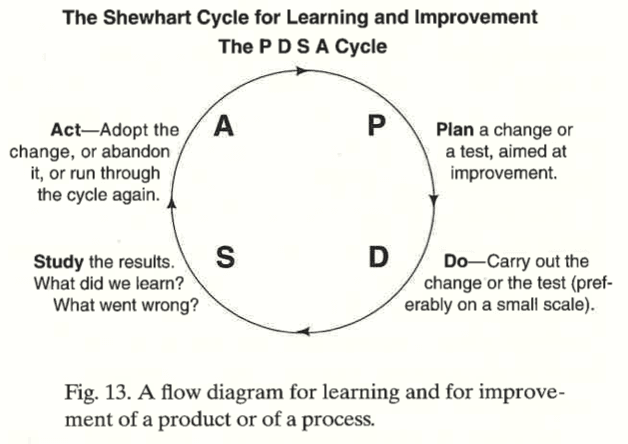
”Askel 1. PLAN. Jollain henkilöllä on idea tuotteen tai prosessin parantamiseksi. Tämä on 0. vaihe, joka on sisällytetty askeleeseen 1. Se johtaa testin, vertailun, kokeen suunnitteluun. Askel 1 on koko jakson perusta. …
Askel 2. DO. Suorita testi, vertailu tai koe, mieluiten pienessä mittakaavassa askeleessa 1. päätetyn suunnitelman mukaan.
Askel 3. STUDY. Tutki tuloksia. Vastaavatko ne toiveita ja odotuksia? Jos ei, mikä meni pieleen?…
Askel 4. ACT. Hyväksy muutos tai Hylkää se tai suorita sykli uudelleen. ” Tämä vaihe vaatii ennustamisen, toteaa Deming
(”PDSA Cycle. This is a flow diagram for learning, and for improvement of product or of process. Step 1. Plan, Somebody has an idea for improvement of a product or of a process. This is the 0-th stage, embedded in Step 1. It leads to plan for a test, comparison, experiment. Step 1 is the foundation of the whole cycle. .. Step 2. DO. Carry out the test, comparison, or experiment, preferably small scale, according to the layout decided Step 1. Step 3. STUDY. Study the results. Do they correspond with hopes and expectations? If not, what went wrong?…Step 4. ACT Adopt the change or Abandon it or Run through the cycle again.”(2) s. 131-133.)
Ei halaistua sanaa poikkeaman syystä, koska sitä ei satunnaissyyperusteisesta ilmiöstä voi löytää! On vain idea, ei siis syytä, ei edes syyhyn perustuvaa ideaa. Laatutaululla ESTETÄÄN satunnaissyyperusteisten ongelmien syiden etsiminen. Ihminen kyllä löytää ”syyn” mihin tahansa ja tekee toimenpiteen, joka johtaa väärään suuntaan. Tämä mahdollisuus on Demingin mukaan 94 %. Laatutaulumenetelmässä (järjestelmässä) on ”pakko” ETSIÄ erityissyyperusteisesta ilmiöstä ja vain näistä syy(juuri) virheen, vian tai hukan ilmenemismuodolle (oireelle) ja tehdä toimenpide. Tämä tapahtuu laatutaulun vieressä olevalla erityissyytaululla. Tämä on laatuteoriaa!
Näille kahdelle luokitteluryhmälle on lukuisia rinnakkaisia nimiä. Katso edellinen artikkeli: Laatutaulu: virheet ja hukka (3). Luokittelu tapahtuu SPC-rajojen, laatutaulussa C-rajan, perusteella.
Jako on äärettömän tärkeä. Jos analysoit ja kosket satunnaissyyperusteiseen poikkeamaan (virhe, vika tai hukka) ja yrität parantaa tuotetta, palvelua tai prosessia, mitä suurimmalla todennäköisyydellä vaihtelu alkaa kasvamaan. Ilmiötä kutsutaan peukaloinniksi eli tamperoinniksi. Tamperointi tuhoaa kaikki parannusyrityksesi! Tamperointia olen käsitellyt artikkelissa: Jatkuvasta tarkastuksesta ja korjauksesta jatkuvaan parantamiseen tai sitten ei? (4).
Kaikissa parannustoimissa – laatu, lean, parhaat käytännöt, pienin askelin parantamisessa jne. – on keskustelussa ohitettu virheellisten tai väärien toimenpiteiden vaikutus. Väitän, että jokaisen toimenpiteen vaikutus on negatiivinen, jos se ei ole positiivinen. Erityisesti W. Edwards Deming painotti negatiivisten vaikutusten estämistä ehkä enemmän kuin positiivisten vaikutusten aikaansaamista!
Edellisessä osassa 1 käsittelin laajemmin laatutaulun teoriaa ja sitä, mihin taulun toiminta perustuu – luonnossa havaittuun tilastolliseen stabiilisuuteen. Yrityksen prosesseja ja niiden tuloksia on arvioitava tätä ilmiötä vasten ja myös spesifikaatioita vastaan. Näitä vertailuja kutsutaan SPC:ksi ja suorituskykyanalyysiksi. Suorituskykyanalyysistä lisää artikkelissa: Prosessin ja työkoneen säätäminen ja asettaminen (5).
Tässä artikkelissa kerron laatutaulun kehityshistoriasta ja tuloksista. Laatutaulun keskeinen ajatus oli tehostaa entisestään tilastollista stabiilisuutta, parantaa laaduntuottokykyä, erityissyiden poistamista ja reagoida käytännön laatu- ja organisaatiohukkiin ja erityisesti estää virheellinen toiminta.
Teoria, käytäntö ja kokemukset on koottu myös kirjaamme Laatutaulu – Tehokas menetelmä laadunohjauksen ja parantamiseen, 2024 (6). Laatutauluilla on voitettu Laatupalkinto vuosina 1986, 1990, 1991, 2000 (Kemppi Oy, 2 x Stala Oy, Salpausselän Kirjapaino Oy). Laatutaulut ja eri versiot ovat käytössä sadoissa yrityksissä ympäri Suomea. Tauluista on tehty myös tietokoneversioita erityisesti niissä tapauksissa, joissa syntyy mitattua dataa (multi SPC).
Historia sinänsä voi olla kiehtovaa tai tylsää, koska se on tai ei ole omakohtaista, mutta se voi kertoa, millaisiin laatu- ja organisaatio-ongelmiin olet ehkä joutunut tai saatat joutua ja kuinka olen yrittänyt niitä ratkaista ja millaisia tuloksia on syntynyt ratkaisujen tuloksena.
Yleiset laatujärjestelmät ja ideat muuttuvat verraten hitaasti. Ehkä kerran pari sadassa vuodessa. Muutoksissa menee joka tapauksessa vuosikymmeniä. ISO 9001, järjestelmää alettiin kehittää vuonna 1979 ja ensimmäiset versiot tulivat vuonna1985 (7). ISO 9001 arvio, että uusin päivitys standardiin on valmis syyskuussa 2026, katso komitean tiedote: https://committee.iso.org/sites/tc176/home/news/content-left-area/news-and-updates/update-revision-of-iso-9001.html.(8) ISO:ssa korostettiin ja korostetaan ennaltaehkäisyn ja jatkuvan parantamisen merkitystä.
Sisältö:
Johdanto
1. Laatutaulun historiasta
I. Kehitysvaihe 1976-1980 Valco/FinnValco Oy
II. Kehitysvaihe 1981-1986 Kemppi Oy
2. Yhteenveto
Lähteet
Seuraavassa Osa 3:ssa
III. Kehitysvaihe 1986-2009 Stala Oy
IV. Kehitysvaihe 1990-1995 Halton Oy
V. Kehitysvaihe 1990-2004 Eimo Oy / Foxconn Oy ja Metsä Botnia Oy
VI. Kehitysvaihe 2010-2017 Lahden Autokori Oy / SOE Busproduction Finland Oy (Scania)
Johdanto
Laatutaulun luominen osui suomalaisen laadun käännekohtaan 1970-1980-lukujen taitteeseen. Tällöin laaduntarkastuksen ja valvonnan rinnalle nousi ajatus ennaltaehkäisystä ja parantamisesta. Voisiko virheille ja vioille tehdä jotain muutakin kuin poimia osat tehokkaasti linjalta ja palveluprosesseissa uusia palvelu, romuttaa tai korjata ja tarjota asiakkaille eripituisia takuuaikoja ja rahallisia hyvityksiä?
Ehkäisy oli 1960-70-luvun uusi aalto. Se muutti voimakkaasti yhteiskuntaa. Tulihan mm. ehkäisypillerit Suomen apteekkeihin vuonna 1962 ja sairaanhoidosta tuli terveydenhoitoa sekä ensimmäinen terveyskeskus syntyi vuonna 1972.
Vielä vuonna 1980 tilastollinen näytteenotto, hyväksymistarkastus AQL (AQL, Acceptance Quality Level) oli ”kova” sana laatumenetelmien joukossa (katso artikkeli: Hyväksymisnäytteenotto) (9). Lukuisissa yrityksissä oli kiertävät laaduntarkastajat, jotka näyttein (AQL) ja pistokokein hyväksyivät tai hylkäsivät toimitus- ja valmistuseriä. Lopputarkastukseen ja sen toimivuuteen panostettiin vahvasti. ”Ohjaus hyvä, valvonta paras” oli ajan fraasi!
Toki edelleen 2020-luvulla tarkastustoiminta on yrityksissä relevanttia, mutta siitä yritetään päästä pois tai ainakin vähentää. Toimittaja tarkastaa osat ja lähettää erän mukana sertifikaatit ja tarkastusasiakirjat ostajalle. Toimittajilta vaaditaan vahvaa näyttöä riittävistä suorituskykyindekseistä (Cp>2, Cpk>1,67). Siis Lean Six Sigman osaamista. Tulli tekee pistotarkastuksia elintarvike-erille ja muille säädellyille tuontitavaroille ja viranomaiset tarkastavat tuotteita, palveluja ja prosesseja. Tämä kaikki on numeerista maailmaa ja ok.
Suuri yleisö tuntee yleensä vain tämän toimintatavan laadun tekemisessä – valvontaa ja tarkastusta. Ongelma tässä ”laatujärjestelmässä” on, että se on aikaa ja resursseja kuluttavaa, kallista ja tehotonta. Tarkastuksen jälkeen virheprosentit pyörivät normaalisti 5-20 % tasossa ja jopa ylikin. 100 % varmuuteen ei tarkastuksella päästä kahdesta syystä. 1) Näytteenotossa tarkastettava ja mitattava erä kasvaa liian suureksi, jos AQL -taso on pieni (<0,65 – 1,5 %). 2) Tarkastus-mittalaitteiden ja visuaalisen tarkastuksen suorituskykyä on vaikea kasvattaa yli 95 % tason. Olemme eläneet virheiden ja ”romujen” keskellä!
Virheiden ja vikojen ennaltaehkäisy laatutoimena oli aivan ”uutta ja kummallista” vuosina 1970-80, jolloin oma laatu-urani alkoi. Minua pidettiin laatupiireissä vähintäänkin höyrähtäneenä, kun esitin tarkastus- ja valvontapäälliköille ennaltaehkäisyajatuksia. Taustani komponentti-insinöörinä ja elektronifyysikkona tuki kuitenkin ennaltaehkäisy- ja parannusajatusta.
Elektroniikan komponenttien valmistuksessa ennaltaehkäisy oli jo tuolloin mielummin sääntö kuin poikkeus. Vastuksia, kondensaattoria, transistoreita, integroituja piirejä tai muuta komponenttia valmistettaessa ei korjauksille ollut sijaa. Niinpä alalla tyypillinen mittari on saanto (yield). Saanto = 100 – virhe %. Mittari kertoo, kuinka paljon saatiin onnistumaan ensimmäisellä kerralla oikein. Transistorissa luku oli vuosina 1960-70 noin 1-5% paikkeilla (95-99% meni hylkyyn, roskiin, hukkaan), mutta kehittyi hyvin nopeasti 95-99,9 % ja ylikin. Ei ole sattumaa, että tässä ympäristössä syntyi Motorolalla Six Sigma -menetelmä vuonna 1979 (10). Tämä loi uudet tavoitteet ja menetelmät laadulle. Virheprosentin on oltava < 3,4 PPM (< 0,00034% tai saantona ilmaistuna >99,9997 %) (10).
Valmistuin Otaniemestä vuonna 1974 elektronifysiikan (puolijohdetekniikan) osastolta ja ensimmäinen työpaikkani elektronifysiikan, radiotekniikan ja säätötekniikan assistentin toimien jälkeen oli Evox Oy tuotekehitys- ja laatuinsinöörinä vuosina 1975-77. Evox Oy valmisti Lohjalla kondensaattoreita miljoonia kappaleita. Näitä ei voinut korjata. Viat oli ennaltaehkäistävä eli saantoa oli parannettava. Onnistuin jo tällöin ennaltaehkäisemään, parantamaan merkittävästi yrityksen saantoa lukuisilla toimilla mm. kehittämälläni ”pin-hole” -mittauksella, joka tapahtui aluminoidun kalvon ”polton” ja leikkaukseen yhteydessä. Laatutaulusta ja SPC.stä ei vielä tässä vaiheessa ollut tietoa.
1. Laatutaulun historiasta
Laatutaulujen kehitysvaiheet voidaan jakaa kuuteen (6) eri vaiheeseen 30 vuoden ajanjaksolle. Kussakin vaiheessa olen pyrkinyt parantamaan laatujärjestelmää – korjaamaan heikkouksia – ja tuomaan uusia ominaisuuksia.
Kehitysvaiheet on tapahtuneet eri yritysten prosesseissa
- Kehitysvaihe 1976-1980 Valco/FinnValco Oy
- Kehitysvaihe 1981-1986 Kemppi Oy
- Kehitysvaihe 1986-2009 Stala Oy
- Kehitysvaihe 1990-1995 Halton Oy
- Kehitysvaihe 1990-2004 Eimo Oy / Foxconn Oy ja Metsä Botnia Oy
- Kehitysvaihe 2010-2017 Lahden Autokori Oy / SOE Busproduction Finland Oy (Scania)
I. Kehitysvaihe 1976-1980 Valco/FinnValco Oy
Laatutaulujen historia juontaa juurensa Japaniin ja Hitachin kuvaputkitehtaaseen, joka toimi kaupungissa nimeltä Mobara, n. 50 km Tokiosta.
Mobara oli elektroniikkavalmistuksen keskittymä. Kaupungissa oli 1970-luvulla noin 60 000 asukasta. Hitachin tehtaat oli suurin työnantaja. Hitachi valmisti elektroniikkakomponentteja LCD:stä ja puolijohdekomponenteista kuvaputkiin. Sain vierailla näissä yksiköissä ensimmäisenä länsimaisena henkilönä ja toimia kaksi kuukautta teknisenä koordinaattorina Valcon ja Hitachin välillä.
Hitachin valtavissa kuvaputkitehtaissa käytettiin 1970-luvulla hyvin yleisesti isoja visuaalisia tauluja ja opasteita, jotka oli kiinnitetty käytävien seinille. Seinät oli käytännössä täytetty erilaisin tauluin ja opastein. Visuaalisuus ja suuri koko on luontevaa Kanji-merkkien kuvakielen yhteydessä toisin kuin meidän kirjoitettu teksti.
Visuaaliset taulut siirtyivät Hitachilta Suomeen Valco Oy:n kuvaputkitehtaalle. Suomen valtio ja Hitachi perustivat kuvaputkia valmistavan Valco Oy:n vuonna 1976. Tehdas rakennettiin Imatralle ja käynnistyi vuonna 1977. Tehdas valmisti Hitachin lisenssillä kuvaputkia.
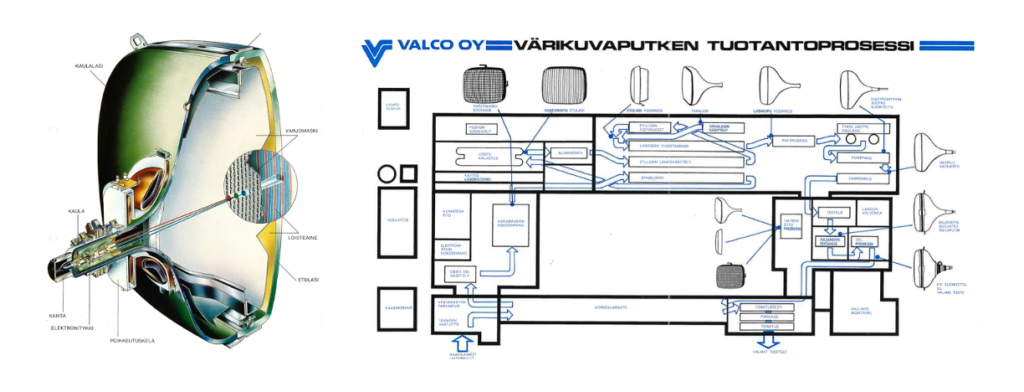
Vuonna 1979 tehtaan nimeksi tuli FinnValco Oy ja sen omistivat Salora Oy (20 %), Suomen valtio (60 %) ja Hitachi Oy (20 %). Tehdas toimi Imatralla ja komponenttitehdas (”tykki” ja varjomaskin kehys) Sotkamossa. Tehtaan pinta-ala 25 000 m2 ja tilavuus 230 000 m3. Henkilöstöä oli noin 350-550 henkilöä. Tehdas toimi keskeytyvässä kolmivuorossa.

Kuvaputki on painava (n. 20-25 kg), räjähtävä TV-komponentti, joka säteilee valmistusvaiheessa ”tappavaa” röntgensäteilyä. Räjähdys sidotaan prosessin viimeisessä vaiheessa räjähdyssuojapannoilla, jonka jälkeen se ei sinkoa laseja ympäriinsä ja sitä ei voi purkaa. Tehdas oli raskasta prosessiteollisuutta, jossa liikkui kuumaa ”lasia” n. 30.000 kg/vuorokausi vakionopeudella (indeksi prosessi, jossa vakiotahdilla kuvaputkiaihio siirtyy vaiheesta toiseen). Indeksi prosessin lopussa 17 s/kpl (≈4000 – 5000 kpl/viikko). Henkilöstön tehtävänä oli ensi sijassa (100-150/vuoro) valvoa prosesseja ja manipulaattoreita ja myöhemmin robotteja (n. 50 kpl).
Työntekijöillä ja operaattoreilla ei ollut prosessissa suoraa kosketusta ja vaikutusta itse tuotteeseen tai sen aihioon, mutta prosessilaitteisiin kylläkin. Lähes kaikki prosessivaiheet olivat säätimien ja parametrien ohjaamia (asetusarvoja).
a) ”Laatutaulun” esivaihe ja rantautuminen Suomeen
Prosessin keskeinen tavoite oli saada onnistumisprosentti, laatu, saanto (yield), mahdollisimman korkeaksi. Saanto määritteli myös myytävien tuotteiden määrän. Prosessin nopeus oli vakio (indeksinopeus n. 17 sekuntia/vaihe) lämpöuuneista ja niiden lämmitysprofiileista ja tyhjöpumppauksesta johtuen.
Prosessin aikana kaikki tuoteaihiot tarkastettiin ja luokiteltiin hyvä/huono visuaalisesti ja samalla poistettiin virheellisiä tuoteaihioita erillisen itsenäisten laaduntarkastajien (QC) toimesta 8:ssa kohtaa prosessia. Tuotteita ei voinut korjata! Jokainen poistettu aihio aiheutti prosessivirtaan ”reiän” eli saanto- ja tuottomenetyksen ja myös materiaalihävikin.
Prosessin tarkastuspisteet ilmenee karkeasti kuvaputken osa (kuvan) kohdalla.
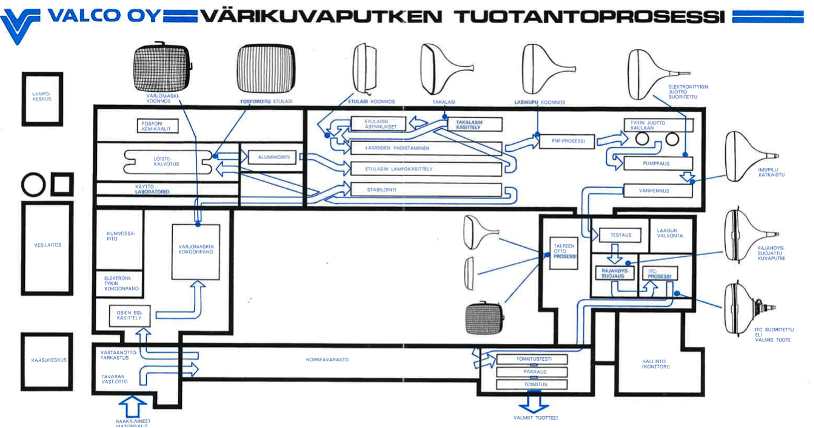
Lopullinen onnistuminen määräytyi lopputestauksessa ja ITC:ssä, jossa asennettiin poikkeutuskela ja säädettiin kuva. Tehtaan alkuvaiheessa valmiit kuvaputket pidetään 1 vuoden varastossa ja tarkastetaan vuoden kuluttua putken sisällä olevan tyhjön pysyvyys. Muistuttaa juuston kypsytysvaihetta! Kun prosessi on hyväksymistestit läpäisyt (putkessa säilyy tyhjö), tuotteet voidaan myydä asiakkaille suoraan.
Jokaisen osavalmistuksen saanto (onnistumisprosentti) laskettiin ja piirrettiin käyräksi. Kuvassa (6) tehtaan käynnistymisestä 1978 maaliskuuhun 1979. Tehdas ajettiin alas 19.12.1980.
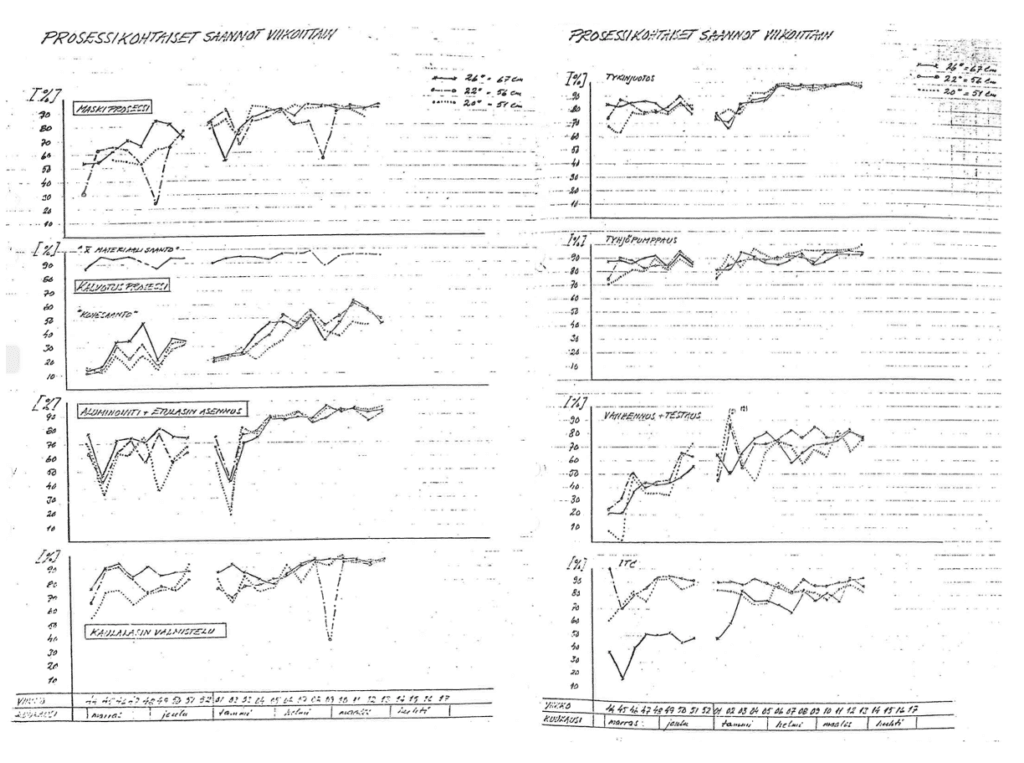
Nousu (parannus) oli vakaata, mutta silloisen ja tämän päivän näkökulmasta ehkä liian hidasta. Lopullinen saanto saadaan, kun vaiheiden saannot kerrotaan keskenään.
Alkuperäinen ongelma oli, kuinka selvittää, mikä ja miksi jokin komponentti/prosessointi oli prosessin aikana hylätty ja mitä olisi tehtävä tilanteen parantamiseksi. Kuinka kasvattaa saantoa lähelle 100 %. Mikä tai mitkä ovat inputteja (juurisyitä) hylkäyksille ja miten näitä pitäisi muuttaa? Vaikuttaako muutos tulevaan saantoon positiivisesti vai huonontaako muutos saantoa? Tätä kutsutaan myös vikojen ennaltaehkäisyksi, tai parannukseksi.
Kuvaputken valmistusprosessi on pitkä ”kokoonpanolinja” jossa kuvaputkiaihioon tuodaan komponentteja ja prosessivaiheita. Korjausmahdollisuuksia ei juuri ollut muualla kuin loistekalvotus- eli ”screening”prosessissa, jossa kemialliset loistekalvot eri väreille luotiin ja valotettiin ”stripit” (nauhat 3 värille). Tässä prosessissa kalvo voitiin pestä ja kalvottaa uudelleen (korjata) ja valottaa. Materiaalihävikki kalvotus-, valotus- ja syövytysprosessissa oli kuitenkin pientä. Tämä prosessi oli pullonkaula!
Jos prosessi tai komponentti oli virheellinen tai prosessissa oli häiriö, se johti kuvaputkiaihion hylkäykseen. Hylkäys johti samalla myös tyhjään tuotantopaikkaan, reikään (se on: tuotantomenetys, valmistusmäärän lasku). Laitteistot toimivat kiinteillä vakionopeuksilla (indeksi). Saanto oli kaiken a ja o.
b) Laadun tarkastajat ja hylkäys/hyväksyminen
Alkujaan prosessissa tapahtuneet hylkäykset (vialliset) etsittiin, ”löydettiin” ja poistettiin laatuosaston tarkastajien toimesta. Tarkastajat toimivat tarkastuspisteissä kolmessa vuorossa. 1970-80-luvulla laadun tekemisen yleinen tapa oli ”tarkasta ja hylkää” vialliset komponentit ja tuotteet itsenäisten tarkastajien toimesta!
Tarkastustulokset koottiin 1970-80-luvun tapaan laaduntarkastajien ja -valvojien toimesta laatuosastolle (QC). Ylemmälle johdolle (johtajat ja päälliköt ) toimitettiin viikoittain raportti kunkin prosessivaiheen saannoista ja hylkäyssyistä ja laajempi raportti kuukausittain. Joitain raportteja myös kone- ja laitehäiriöistä.
Yksittäisten kuvaputkiaihioiden vikojen ja hylkäysten tarkastelusta ei ollut hyötyä, vaikka sitäkin yritettiin tehdä niin suomalaisten kuin japanilaisten prosessi-insinöörien ja -teknikoiden toimesta. Ei näkyvää tulosta! (Työntekijä ei saanut muuttaa asetusarvoja! Työntekijät saivat vain korjata konehäiriöt ja rikot. Prosessi-insinööri sai muuttaa asetusarvoja, mutta millä tiedolla!)
Tieto virheistä (saanto) onnistumisista ja hylkäyksistä oli strategisesti ja liiketaloudellisesti huippusalaista ja raportit olivat salattuja. Ulkopuolinen kilpailija saattoi helposti laskea yrityksen tuotantomäärät, kustannukset ja kilpailukyvyn näistä arvoista. Siksi tiedot ”salattiin” ja yhteenvedot toimitettiin vain johdolle. Minulla oli poikkeuksellisesti tarkat tiedot, koska olin vastuussa mm. lopputarkastus-aluetta yhdessä QC:n kanssa ja sain tiedot suoraan sieltä.
Tämä laaduntarkastajien järjestelmä (QC) – tarkasta ja hylkää – osoittautui hitaaksi ja toimimattomaksi – ja oli kallis. Seurauksena tästä oli myös, että työnjohto ja työntekijät eivät voineet seurata tilanteen kehittymistä ajantasaisesti ja arvioida tehtyjen toimenpiteiden, konerikkojen ja -korjausten, onnistumista.
Tarkastuspisteissä havaittujen virheellisten määrä ylösajossa oli niin vähäinen (1-5 kpl/virhetyyppi/vuoro), että siitä ei voinut päätellä kehityssuuntaa, saati mitä voidaan tehdä/ennustaa virheiden ehkäisemiseksi etenkin, kun edellisen vuoron työn tulos tuli seuraavalle vuorolle (prosessihitaus). Ei ollut tietoa ja taitoa, saati teoriaa, kuinka virheet voidaan ennaltaehkäistä ja saantoa parantaa edes pienin askelin.
Johtopäätös: Tarkastus ja hylkäys karsi viallisia (ja ei viallisia?), mutta ei parantanut saantoa (yield)! Raportointi ylimmälle johdolle eivät myöskään parantaneet saantoa. Se oli vain informaatiota. Miten voisi parantaa toimintaa? Koko muu henkilöstö oli kasvanut ”tarkasta ja hylkää” kulttuuriin.
c) Laatuinformaation jako työnjohdolle viikoittain
Elo-syyskuussa 1978 siirryttiin järjestelmään, jossa laadunvalvontaosasto (QC, Quality Control) jakoi informaation virheistä joka viikko kullekin 6-7 työnjohto-alueelle taulukoiden muodossa (esimerkki yhdestä taulukosta, kuva) siinä toivossa, että tehdään nopeampia ja tehokkaampia toimenpiteitä vikojen poistamiseksi ja saannon ja määrän kasvattamiseksi.
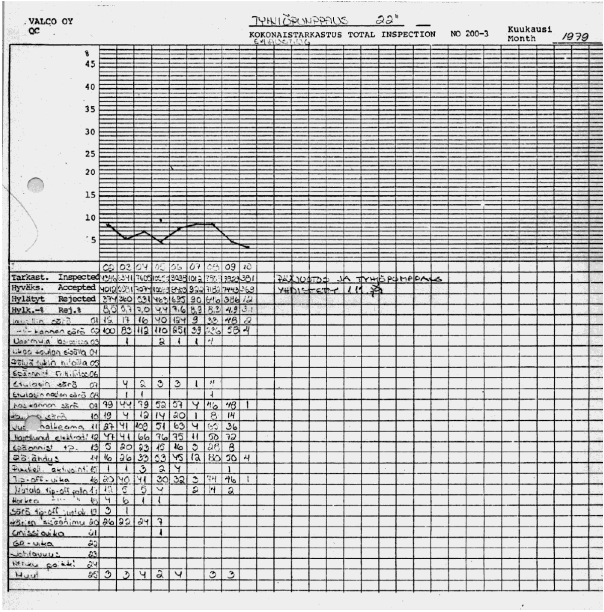
Järjestelmä oli edelleen liian hidas ja epämääräinen ja kohdistui yksittäisiin tapahtumiin. Taustalla oli myös vanha ”tayloristinen ajatus” virheiden ja vikojen syystä: laiskuus ja huolimattomuus. Virheet johtuvat ensi sijassa tuotanto-henkilöstön huolimattomuudesta ja välinpitämättömyydestä (konerikkoja kohtaan). 1970-80-luvun mantraa!
Huolellisuusnumero (arviointi) oli jokaisen oppilaan todistuksessa 1960-80-luvulla. Oli huolellisia ja huolimattomia oppilaita ja tietysti huolellisia ja huolimattomia työntekijöitä! Huolelliset työntekijät eivät tehneet virheitä. Huolimattomat työntekijät tekivät kaikki virheet! Johtaminen ja valvominen kohdistettiin huolimattomiin (ja laiskoihin) työntekijöihin. Jokainen arvaa, miten!
Johtopäätös: Edelleen liian hidas palauteinformaatio
d) Laatuinformaation jako työnjohdolle päivittäin
Viikoittaisesta järjestelmästä luovuttiin ja laatuosasto ja laadun valvojat, jotka olivat oikeutettuja tarkastamaan ja hylkäämään kalliin kuvaputkiaihion, alkoivat toimittamaan päivittäin vika- ja hylkäysinformaatiota suoraan työnjohtoalueille.
Ongelmana tässä oli, että informaatiota ei voinut kohdistaa vuoroille. Tehdas toimi kolmessa vuorossa ja informaatio yhdessä vuorossa. Työnjohto ja työntekijät eivät voineet (ja eivät halunneet?!) perehtyä vikoihin ja hylkäyksiin tarkasti ja niihin olosuhteisiin, inputteihin (mahdollisiin kone tai laiterikkoihin), joissa viat tapahtuivat etenkin, jos toinen vuoro oli ne tehnyt. Kukapa toisen virheitä haluaisi tutkia! Asetusparametrit olivat edelleen tuotantoinsinöörien takana ja muutettavissa ja vaativat muutettaessa erityisen hyväksymisprosessin. Liittyy tyhjöprosessiin ja tyhjön (10-10 Torr) säilymiseen.
Yleensä jokin poikkeama oli tapahtunut prosessissa. Jokin asetus oli muuttunut, prosessissa oli hetkellinen vika, lämpötila vaihdellut, polttimen liekki huono, kuljetin nykinyt, mutta sen yhteyttä (kausaalisuutta) tuotteeseen ei yleensä pystytty itse tuotteesta havaitsemaan kuin vasta testausvaiheessa, kun putkeen saatiin kuva ja mittausarvot, jos silloinkaan. Työntekijän valvonta-ala oli n. 200 – 1000 m2/henkilö. Lähes koko prosessin ajan putkiaihio oli suojien ja prosessikoneiden (uunien) sisässä tai kattokuljettimilla, joihin ei nähnyt.
Tarkastus tapahtui 12-16 tunnin kuluttua prosessin suorittamisesta. Lasi saattoi olla kuuma 400-500 °C ja vaati jäähtymisen tai kemikaalit tarvitsivat kuivumisajan.
Työnjohto ei myöskään muistanut, mitä vikoja (so. prosessihäiriöitä) vuorossa oli tapahtunut.
Johtopäätös: Nopea informaatio ilman kohdistettua tietoa ei toiminut!
e) Laatuinformaation keräys ja jako työntekijöille. Laatutaulun esiaste on syntynyt!
Tässä vaiheessa syntyi uusi organisoitu tapa selvittää tuotannossa tapahtuneita häiriöitä, hylkäyksiä ja vikoja.
Uusi tapa syntyi, kun olin Japanissa Hitachin tehtaalla 5.1.-3.3.1979 kahden kuukauden ajan ns. teknisenä koordinaattorina ja näin japanilaisten insinöörien ja teknikoiden tavan toimia. Olin yhtenä jäsenenä tässä ryhmässä. Vastuu ja toiminta oli organisoitu eri tavoin kuin Suomessa oli totuttu elektroniikka ja konepajoissa toimimaan 1970-luvulla.
A3-kokoiset työnjohdon mapissa olleet pienet virhelistat/taulut (8×3=24 kpl), joita laatuosasto oli toimittanut, siirrettiin laatuosaston ylläpitovastuulta tuotannon vastuulle kuten Hitachilla. Tämä oli suuri ja ennenkuulumaton muutos 1970-luvun lopussa!
1980-luvulle asti on laadun organisoinnissa vannottu tuotannosta riippumattoman laaduntarkastuksen ja valvonnan nimeen. Tämä malli ei toimi parannuksessa ja ennaltaehkäisyssä, mutta on erinomainen ja objektiivinen valvonnassa ja tarkastuksessa.
Jos halutaan tuotanto-organisaation ja työntekijöiden ohjaavan ja parantavan toimintaa ja laitteita, on heidän tiedettävä, mitä ohjata ja parantaa. Tämä on myös Demingin oppi. Erityissyyt eli stabiilisuuden ohjaus ja parantaminen kuuluu tuotannolle. Aina 1980-luvulle asti ohjaus ja parannus nähtiin vähämerkityksellisenä keinona laadun tekemisessä.
Uudessa tavassa työntekijät ja työnjohto määritteli viallisen ja hylättävän osan ja merkitsi joka vuoro henkilökohtaisesti isolle A0-kokoiselle taululle kaikki vuoron aikana eri syistä tapahtuneet viat, virheet (poikkeamat) ja prosessihäiriöt oireluokituksen ja esiintymismäärän mukaisesti.
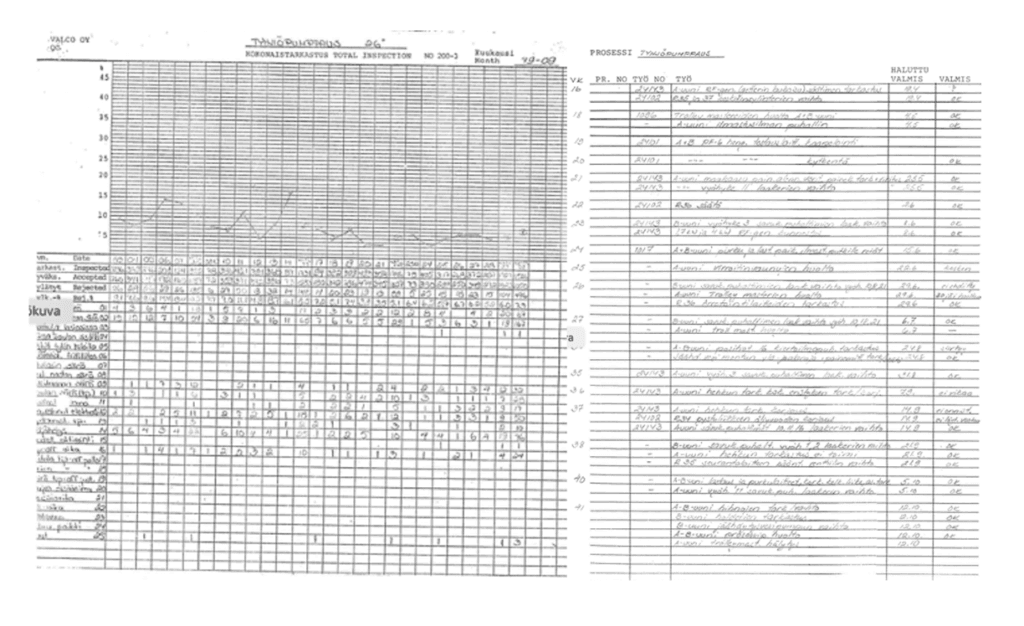
Koko osaston ja kaikki työntekijät näkivät kaukaa, mikä oli laatutilanne ja prosessin ohjaukset ja korjaukset, missä on virheitä ja häiriöitä.
Menettelyllä kukaan ei voinut väittää, että ei tiedä viasta ja hylkäyksestä ja korjauksen tarpeesta. Tuotannon henkilö oli omakätisesti kirjoittanut vian tai häiriön erityiselle keräyslistalle tukkimiehen kirjanpidolla ja työnjohto siirsi viat ennen vuoron päättymistä taululle joko numeroin tai tukkimiehen kirjanpidolla.
Menettely oli tarkasti määritelty. Työntekijä (prosessin hoitaja) tuo tiedon kirjattuna ja antaa sen työnjohdolle, joka kirjaa tuloksen ITSE taululle. Huomaa kaksivaiheinen kirjaus, jonka keksin, jotta työnjohto ei voi sanoa, ettei tiennyt vioista. Puhe hyvä, kirjaus parempi!
Koko ketju tiesi tasan tarkkaan, mitä oli tapahtunut, minä hetkenä oli tapahtunut, mitkä olivat olosuhteet ja siitä oli dokumentoitu jälki. Pulinat loppuivat!
Edelleen tämän rinnalla toimi itsenäiset laaduntarkastajat (valvojat), jotka tarkastivat, luokittelivat ja ”mittasivat” jokaisen osavaiheen laadun. Myös nämä tiedot tulivat taululle. Näistä tauluista luotiin laatuosaston toimesta viikko- ja kuukausitilastot ja käyrät.
Laatuosasto ja tarkastajien, laadunvalvojien, rooli ja asema muuttui valvojasta varmistajaksi ja tuotanto oli itse vastuussa laadusta (stabiilisuudesta) ja tehdyistä toimenpiteistä. Tämä oli uutta ajattelua! Ei helppo muutos palkkaneuvotteluineen.
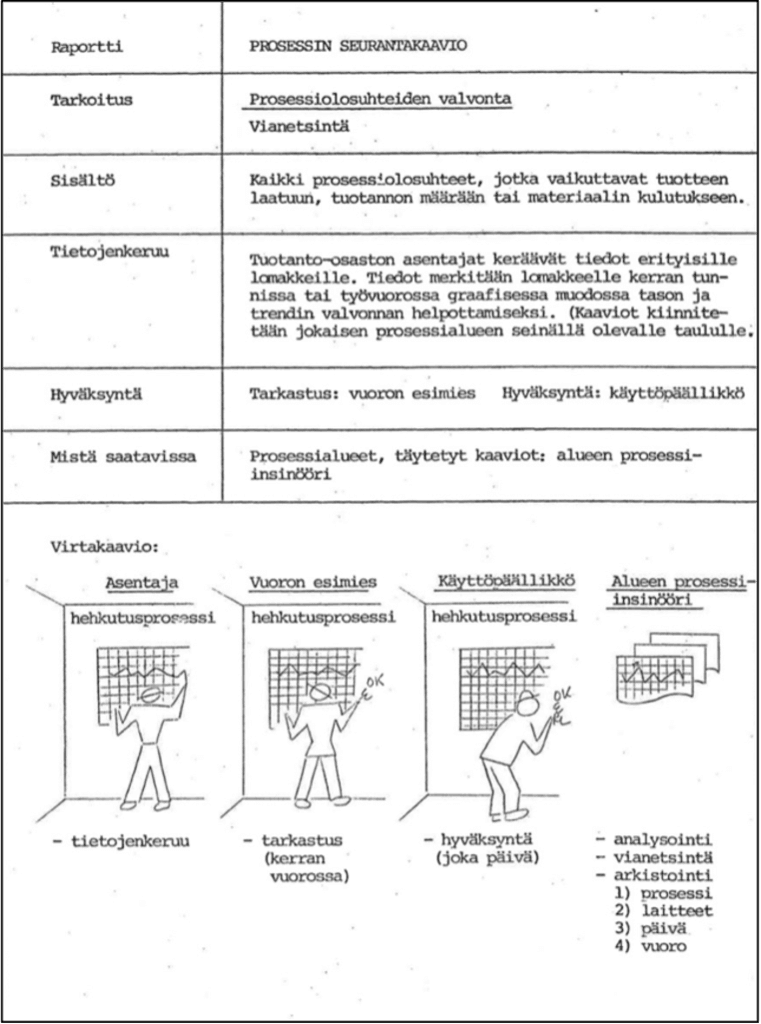
Kehitetty menettely oli menestys, joka näkyi välittömästi helmi-toukokuun 1979 saantokäyrissä (kuva 5) ja hukan voimakkaana vähenemisenä kohti tavoitetta (kuva 8).
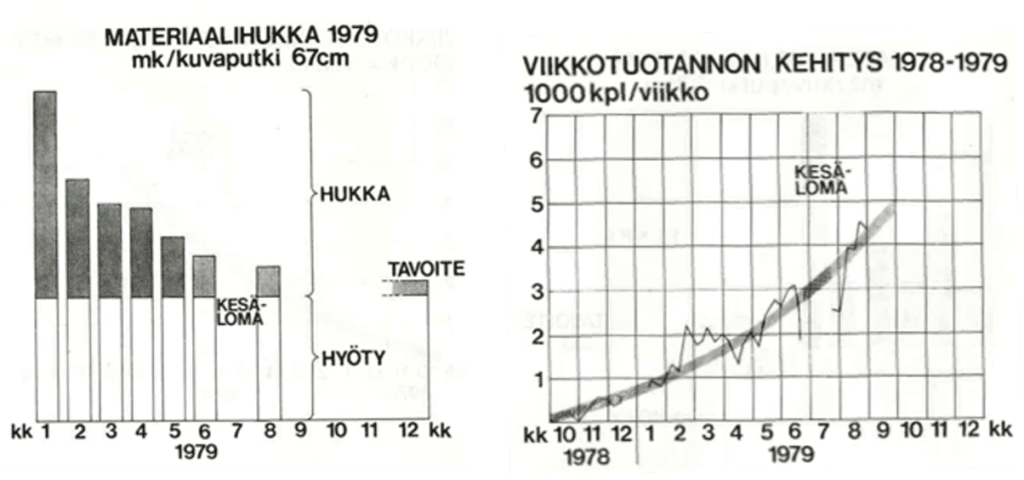
Kuvaputkituotannon saannot paranivat tasaisesti useissa vaiheessa lähelle 98-99 %:tia ja jopa ylikin.
Tehtaan kokonaissaantotavoitteeksi asetettiin vuonna 1977 saanto >80 % 16:sta perättäisen pääprosessin osalta, jolloin yksittäisen prosessin saannon on oltava yli 98,7%. (0,98716=0,811). Saannon paranemien oli suoraan suhteessa määrään. Määrässä päästiin lähelle tehtaan maksiminopeutta 5000 kpl/viikko (n. 350 000 kpl/vuosi) jo vuonna 1979 ja vähän ennen tehtaan lopettamista joulukuussa 1980.
Tehdas lopetettiin toimitusjohtaja Lauri Saaren kirjan ”Valcoinen kirja” mukaan teollisuuspoliittisista syistä joulukuussa 1980 ”Kuvaputkitehdas oli kannattava lopetettaessa!” (11 s. 139-148).
Pasi Nevalaisen kirja ”Epäonnistumisen anatomia – Kuvaputkitehdas Valcon nousu ja tuho 1976-1980” 2022 (12) kuvaa teollisuuspoliittista puolta prosessissa.
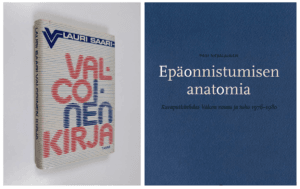
Johtopäätös: Laadun parannus ja ehkäisy toimii vain, kun tuotanto (työntekijä) on suoraan vastuussa virheistä ja vioista ja voi välittömästi tehdä toimenpiteen. Yksittäisten vikojen kokeminen ja näyttäminen ei johda parannukseen.
Yhteenveto
Vielä tässä vaiheessa ei ollut SPC-teoriaa (rajoja), joskin taulut (vuoro, päivä ryhmittely) ohjasivat tietämättämme toimimaan lähes oikein. Jos SPC olisi ollut tiedossa ja käytössä, ylös ajon nopeus olisi ollut ehkä 2-5 kertaa nopeampi!
Miksi ei SPC:tä? Ei tullut mieleen eivätkä japanilaiset asiantuntijat kertoneet.
Ehkä Hitachi ei tiennyt tai ei käyttänyt SPC:tä tai salasivat sen käytön. Manuaaleissa ja ohjeissa siitä ei ollut mainintaa. SPC:n kulta aika alkoi länsimaissa vasta 1980-luvun puolivälissä lähinnä W. Edwards Demingin kirjoitusten, puheitten ja suosion myötä.
Nämä samat SPC-opit Deming oli kertonut japanilaisille 1945-1950, ehkä myös Hitachin johdolle.
Kokemus ei koskaan korvaa hyvää teoriaa! Kokemusta kertyi, mutta ennaltaehkäisyn ja parannuksen teoria puuttui. Uskon, että silloinen johto ei ymmärtänyt valvonnan ja tarkastuksen ja ennaltaehkäisyn ja parannuksen radikaalia eroa toisistaan. Numeerinen maailma ja analyyttinen maailma!
II. Kehitysvaihe 1981-1986 Kemppi Oy
Laatutaulujen toinen vaihe käynnistyi vuonna 1981, kun Kemppi Oy:lle Lahteen rakennettiin laadunohjaus, parannus- ja mittausjärjestelmä (laatujärjestelmä). Siirryin Kempin palvelukseen laatu- ja työsuojelupäälliköksi kesällä 1981.
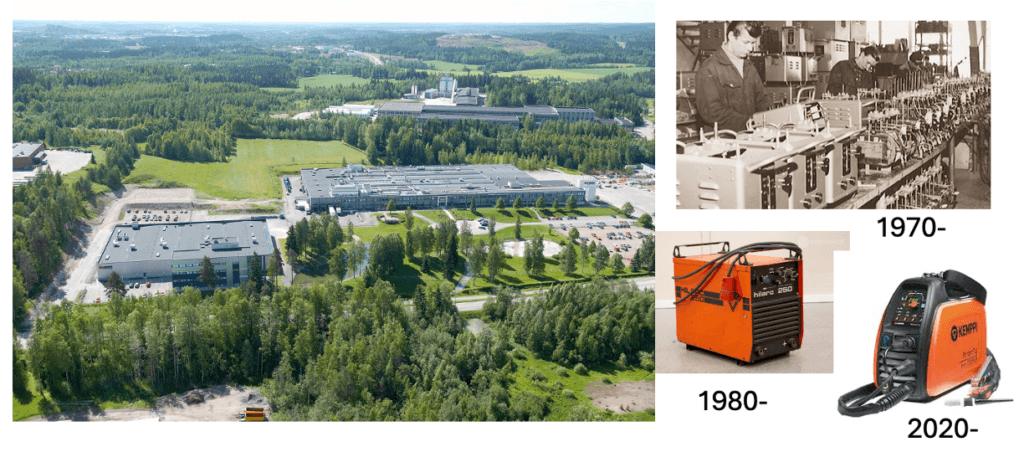
Kemppi Oy valmisti ja valmistaa erilaisia hitsauskoneita ja laitteita ja niissä tarvittavia metalli- ja sähkökomponentteja. Yrityksessä oli hitsauskoneiden kokoonpanolinjat (7 kpl) 1980-luvulla. Henkilöstöä n. 350-450. Tehdas sijaitsee Lahdessa. Perustettu vuonna 1949.
Hitsauskonetehdas eroaa kuvaputkitehtaasta merkittävästi. Kuvaputkien valmistus on prosessiteollisuutta, jossa operaattorit pääosin valvovat prosessilaitteistoja ja heidän työsuorituksensa ei suoraan vaikuttanut tulokseen.
Hitsauskonetehtaassa valmistetaan osia ja sähköisiä komponentteja, jotka asennetaan kokonpanolinjoilla erilaisiin hitsauskoneisiin. Osien määrä vaihteli silloin 50-1500 välillä eri konemalleissa.
Hitsauskonetehtaassa työntekijällä on suora vaikutus tulokseen ja laatuun joko osien valmistamisen tai kokoonpanon kautta. Kuvaputkitehtaassa tehtiin 3 tuotetta (20”, 22” ja 24” kuvaputki), kun taas hitsauskoneita ja laitteita oli yli 50 tuotannossa.
Tuotanto oli järjestetty sarjoiksi, joita tehtiin vierekkäisillä kokoonpanolinjoilla. Työ oli pääosin urakkatyötä, jossa työ annettiin työmääräinten muodossa työntekijälle (työmääräin oli tuotannon ohjauksen ja -suunnittelun kortti, jossa kerrotaan osan tai asennuksen työ, aika, urakka ja muut yksilöintitiedot). Kuvaputkitehtaalla tehtiin tuntityönä putket.
Kempin taulut pohjautuivat ”uuteen” SPC-teoriaan, jonka olin lukenut Juranin Quality Control Handbookista Third Edition 1974, (13), jota on kutsuttu Laaturaamatuksi.

”Raamatun” työnsi käteen silloinen Kempin toimitusjohtaja DI Sakari Raevaara ensimmäisenä työpäivänä 15.8.1981. Olin Sakun suorassa alaisuudessa. Nyt tuli teoria! Hän myös ”passitti” minut välittömästi silloisen INSKO:n pitkälle Laatutekniikan peruskurssille. (INSKO, Insinöörijärjestöjen koulutuskeskus). Kiitos Sakulle! Kurssi uudistettiin ja siirrettiin Laatuyhdistykselle 1983-84 ensin Laadun ABC -kurssina ja sittemmin Laatupäällikkö-kurssina. Kurssi siirtyi edelleen TKK:n (Aalto yliopiston) Master of Quality -kurssiksi. Olin muotoilemassa näitä kursseja. Kurssit saivat vaikutteita Kempillä pitämistäni kursseista. Olin yksi opettajista n. 20 vuotta.
Laatutaulujen kehitykseen kuului niin fyysiset taulut, menettelyt kuin myös informaatio ja koulutus, jota annettiin laatutaulujen yhteydessä. Kempin laatujärjestelmä perustui 1970-luvun tapaan kiertäviin itsenäisiin laadunvalvojiin, lopputarkastukseen ja reklamaatioiden analysointiin. Paljon ennakkoluuloja ja vakiintuneita käytäntöjä oli muutettava Kempillä liittyen virheisiin, vikoihin, niiden syntyyn, keräykseen ja analyysiin.
Kemppi oli ajautunut syviin laatuvaikeuksiin toimimattoman järjestelmän vuoksi!
Reklamaatioiden ja takuukorjausten määrä kasvoi vuosi vuodelta 0,6 %:sta 1,5 %:iin (kasvu 150 %:ia) liikevaihdosta laskien (1975 – 1981), vaikka jokainen reklamaatio (takuukorjaus korjauksen ja osavaihdon tai muun syyn lisäksi) tutkittiin, analysoitiin ja tehtiin toimenpiteitä tehostetusti, jotta vikojen esiintyvyyttä voi vähentää. Noin 30 000 reklamaatiota/vuosi tutkittiin, joka vastasi kappalemääräisesti laskettuna >100 % 1 vuoden takuuajalla. Korjausurakkaa hoiti valtuutetut huoltokorjaamot. Jokainen reklamaatio ja korjausilmoitus meni vastuuinsinöörille, joka tutki ja esitti jokaiseen korjaustoimenpiteen (”parannuksen”?).
Tämä järjestelmä oli muutettava. Toimenpiteitä johti evp majuri Eero Taipale rautaisella otteella ”ratsupiiska” kädessä. Ei jäänyt yhtään korjausilmoitusta ja reklamaatiota tutkimatta ja toimenpidettä tekemättä!
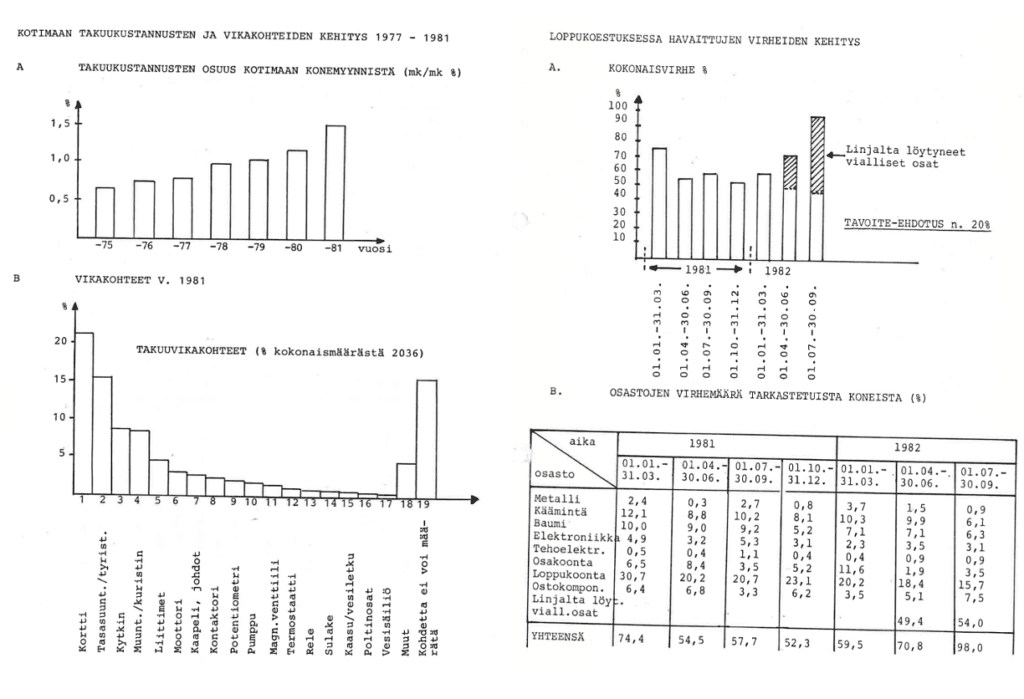
Tänään tiedämme, miksi reklamaatiot kasvoivat 1970-luvulla. Ei noudatettu ohjetta: Ohjaa sisäänmenoja, älä ulostuloa. Tästä ulostulo-ohjauksesta seuraa tampering eli yliohjaus mitä suurimmalla todennäköisyydellä! Ilmeisesti kenenkään ei tullut ajatusta, että virheellinen analyysi ja toiminta johtaa myös muutokseen tosin väärään suuntaan – ja vielä suurella todennäköisyydellä (>94 %).
Kempillä lopetettiin vuonna 1982 takuuvikojen ja reklamaatioiden tutkiminen ja selvittäminen! Oli ilmeistä, että takuu- ja reklamaatioanalyysit ja toimenpiteet olivat virheellisiä. Tämän korvasi laatutauluihin perustuva järjestelmä.
Yrityksestä puuttui ohjauksen ja parannuksen teoria, idea siitä, mitä on ohjattava ja mitä ei saa ohjata ja kuinka ohjaus ja parannus toimii. Kuinka vaikuttaa virheisiin, vikoihin ja takuuseen, reklamaatioihin etukäteen eli ennaltaehkäisten.
Uuden järjestelmän rakentaminen perustui 24.8.1981 päivättyyn tekemääni ”tutkimusraporttiin”, jossa verrattiin erilaisia informaation keräys- ja analyysi-menetelmiä toisiinsa (Juran: Quality Control Handbook, Third Ed).
Seuraavassa otteita raportista:
”VIRHEILMOITUSMENETTELYSTÄ JA TAKAISINKYTKENNÄSTÄ”
Sisäisten virhekustannusten laskennan tarkentamiseksi ja linjalla ja osavalmistuksessa tapahtuvien virheiden vähentämiseksi on virheistä saatavaa tietoa parannettava. Yleisesti (silloin 1981) käytössä olevia järjestelmiä olivat mm:
1. Virhe- ja korjausilmoituslomakkeet
2. Materiaalin kulutuskertoimiin ja työmääräimiin perustuvat järjestelmät
3. Erilaiset valvontatauluihin perustuvat järjestelmät yhdistettynä työmääräimiin
4. Muistinvaraiset, ei kirjalliset, menetelmät
Valittaessa järjestelmien välillä on tarkasteltava niiltä vaadittavia ominaisuuksia:
1. Identifiointitieto = missä virhe on (osa, kohta)
2. Valmistusvaihe, missä virhe on syntynyt
3. Viimeinen suoritettu työvaihe
4. Virheen aiheuttanut osasto
5. Korjaukseen kulunut työaika
6. Virheen kokonaiskustannukset
7. Määrätietoja = virheen laajuus
8. Antaa systemaattisella tavalla varmaa tietoa henkilöille, jotka voivat vaikuttaa laatuun
9. Ajankohtaisuutta (virhetilasto jatkuvasti näkyvillä)
10. Motivoiva ja tavoitteellinen, virheitä vähentävä
11. Työntekijöitä itseohjaava (positiivinen)
12. Kokemuksia ja osaamista taltioiva ja säilyttävä
Edellä olevia kahdellatoista kohdalla analysoin neljää erilaista järjestelmää:
- Virhe ja korjausilmoituslomake, 2. Materiaalikulutuskertoimet ja työmääräimet, 3. Valvontataulut ja työmääräimet, 4. Muistinvaraiset järjestelmät.
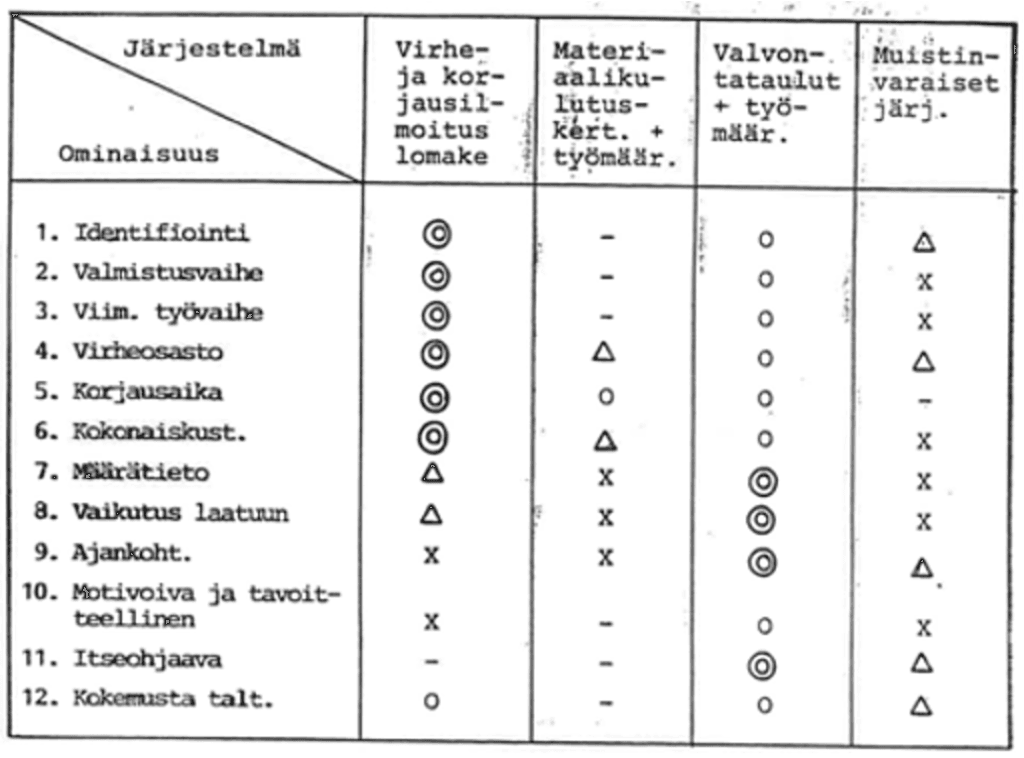
Häränsilmä= erittäin hyvin, O= hyvin, D= tyydyttävästi, X= huonosti, – =ei täytä
Parhaimmin kattaa esitetyt vaatimukset virhe – ja korjaus-ilmoitusjärjestelmät ja valvontataulujärjestelmät. Valituksi tuli valvontataulut, joita myöhemmin alettiin kutsua laatutauluiksi (positiivisempi ilmaisu).
Raportissa luotiin pohja menetelmälle, joka motivoi ja ohjaa henkilöstöä laadun ohjaukseen ja parannukseen ja täyttää laatumittauksen vaatimukset.
Kemppi Oy:ssä lähdettiin siitä ajatuksesta, että seurantajärjestelmää pitää pystyä hyödyntämään perinteisen virhekirjauksen ja sillä kerättävän raportointitiedon lisäksi myös nopean, lähes välittömän palautteen antamiseen henkilöstölle, jotta toimintaa voidaan parantaa.
Raportissa kirjoitin ja kuvasin, että
Valvontataulut + työmääräimet:
Järjestelmä perustuu erilaisiin kaikkien työntekijöiden nähtävissä oleviin valvontatauluihin (=laatutaulu), joihin on merkitty päivittäin työnjohtajien, tarkastajien ja työntekijöiden toimesta tuotantomäärään, laatuun ja materiaalin kulutukseen liittyvät tiedot.
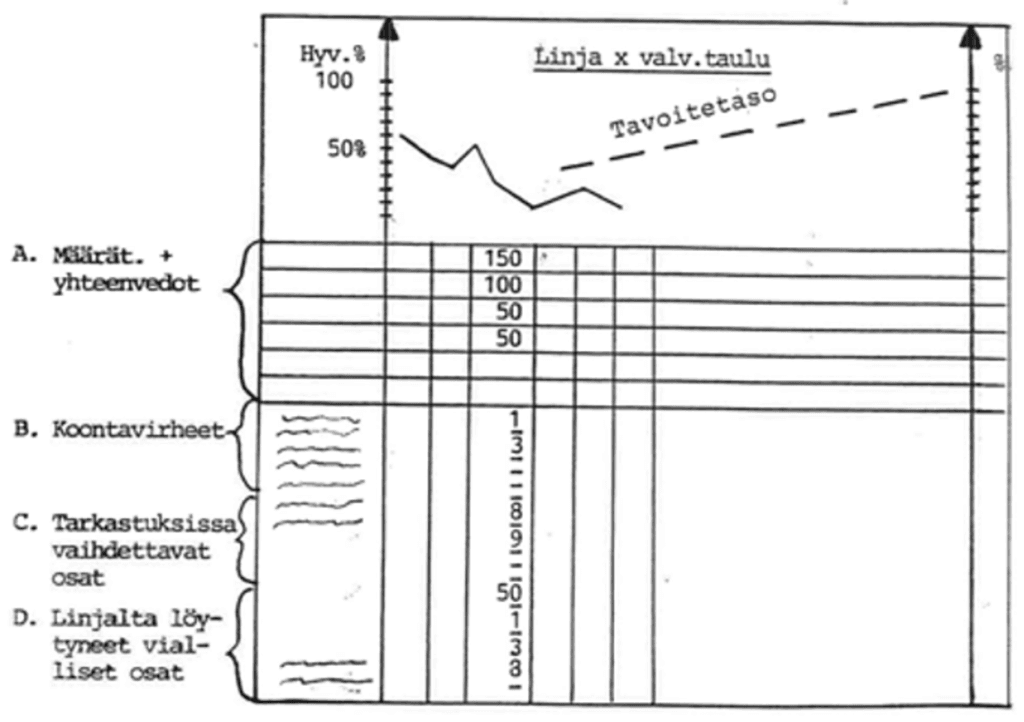
Raportissa oli myös ehdotus kokeilusta ja käyttöaikataulusta ja tavoitteet. Huomaa PDSA-malli kehittämisessä:
”Ehdotus valvontataulujen kokeilu- ja kehitysaikatauluksi:
1. Valitaan 1. kokoonpanolinja, jolla taulua kokeillaan
a. Tarkastaja halukas edelleen kehittämään sopivat virheluokat, osat
b. Linja työntekijät eivät ole vastakarvaan
2. Kehitetään taulua ja merkintöjä ko. linjalla noin 1-2 kk.
3. Päätetään, onko systeemi toimiva vai ei
4. Jos systeemi on toimiva, laajennetaan taulut kattamaan kaikki linjat (1-2 kk)
5. Linjojen kokemuksia hyväksikäyttäen kehitetään osasto kerrallaan sopiva valvontataulusysteemi (3-6 kk)
Tavoitteet, joihin ko. kehityksellä pyritään:
1. Saadaan laskettua sisäiset virhekustannukset.
2. Pudotetaan oleellisesti lopputarkastuksessa havaittuja virheitä (74 % -> <10 %)
3. Aktivoidaan työntekijöitä ja valmistellaan laatupiiritoimintaan
Raportin ohjelma toteutettiin kokonaisuudessaan ja keväällä 1982 siirryttiin laatutaulujen käyttöön kokoonpanolinjoilla. Tauluja (88 cm x 133 cm) oli loppukokoonpanossa ja tarkastuksessa 8-10 vierekkäin 1/kokoonpanolinja ja muuntaja, johtosarja ja elektroniikkaosastolla. Yhteensä 12-13 kpl.
Loppukokoonpanon tauluihin tuotiin/yhdistettiin myös muiden osavalmistusten virheet ja kaikki linjalta löydetyt vialliset osat.
Laatutauluista puuttuivat edelleen SPC-rajat (C-rajat). En vielä silloin laittanut rajoja näkyviin, vaikka laskin rajat ja toimin niiden mukaisesti. Työnjohto kokoontui tauluille joka päivä n. 15:00, jolloin virheet merkattiin tauluihin, siis ennen työpäivän päättymistä. Tuotanto ”luovutti” minulle ja tuotantojohdolle koko tehtaan sisäisen laadun.
Tarkistin tuloksen ja osoitin ja ympyröin tauluihin erityissyyt joka päivä 5 vuoden ajan ja ”nakitin” työnjohdon. Tämä oli erään tyyppistä sisäistä reklamointia! Hyvin usein tuotannon johto oli kokouksessa mukana ja merkitsi ”japanilaiseen tapaan” kommentit tauluihin. Vastuutyönjohtajat raportoivat tehdyt toimenpiteet seuraavana päivänä tässä laatutaulukokouksessa. En ottanut vastaan tekemättömiä toimenpiteitä! Tähän Kempillä oli totuttu majuri Taipaleen aikana. Erilliset erityissyytaulut puuttuivat. Toimenpiteet kirjattiin suoraan tauluun. Joitain merkintöjä näkyy kuvassa 16.
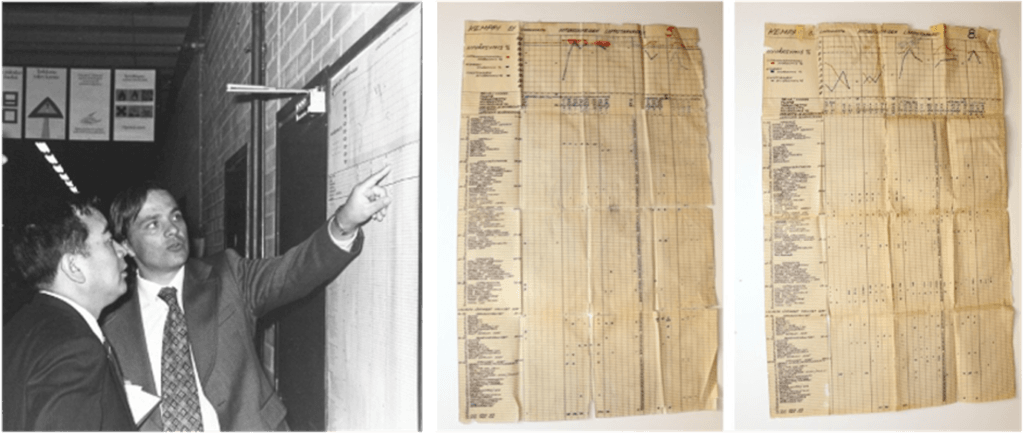
b) Tulokset ja kokemukset laatutaulusta
Kempillä jokaisella oli laatutaulujen käyttöönoton jälkeen oikeus hylätä osa tai edellisen vaiheen työsuoritus. Hylkäysoikeuden voi kumota vain toimitusjohtaja. Tämä ”käsky”kirjattiin Kempin Laatupolitiikkaan!
Huomaa, että tämä oli käänteinen toimintatapa ennen vuotta 1981 vallitsevaan tilanteeseen niin työntekijöiden kuin johdonkin osalta: työnjohdolla oli silloin oikeus hylätä osa tai työ ja myös päinvastoin hyväksyä työntekijän mielestä virheellinen osa tai työ. Työntekijän oli noudatettava työnjohdon päätöstä. Hänellä ei ollut oikeutta kumota johdon kantaa. Työnjohdon kannan pystyi silloin kumoamaan vain laadunvalvontapäällikkö.
Työntekijän hylkäyskieltoa perusteltiin säästösyillä – kyllä huonompikin materiaali kelpaa, tee vain! Laatufilosofiassa oli vannottu tuotannosta riippumattoman laadunvalvonnan nimeen. Jos vanha käytäntö olisi jätetty voimaan, yhtään virhettä ja merkintää ei olisi tullut laatutauluille!
Kempin organisaationkulttuuri oli vahvasti virheitä vastaan, hyvä niin, mutta se samalla johtaa virheiden kätkemiseen ja itsensä pettämiseen. Virheelliset ja vialliset osat laitettiin koneisiin kiinni. Urakkapalkkauksessa jokaisesta valmiista työkappaleesta sai tietyn summan, oli se hyvä tai huono. Korjaus ”söi” valmistuneiden määrää ja alensi urakkapalkkaa.
Käyttöönotetut laatutaulut saivat aikaan radikaalin laadun parannuksen (kuva 17) samalla, kun tuotanto laajeni:
- Takuuviat puolittuivat noin 2 vuodessa (alkuperäinen pääongelma), kokonaislaatukustannukset kääntyivät laskuun, kokoonpanon virheet vähenivät.
- Muuntajien sisäinen virheprosentti putosi 12-15 %:sta 0%:iin. Tällä oli suuri vaikutus. Ennen hitsauskonetta sanottiin hitsausmuuntajaksi. Muuntaja oli hitsauskoneen pääkomponentti, kunnes elektroniikka syrjäytti sen roolia.
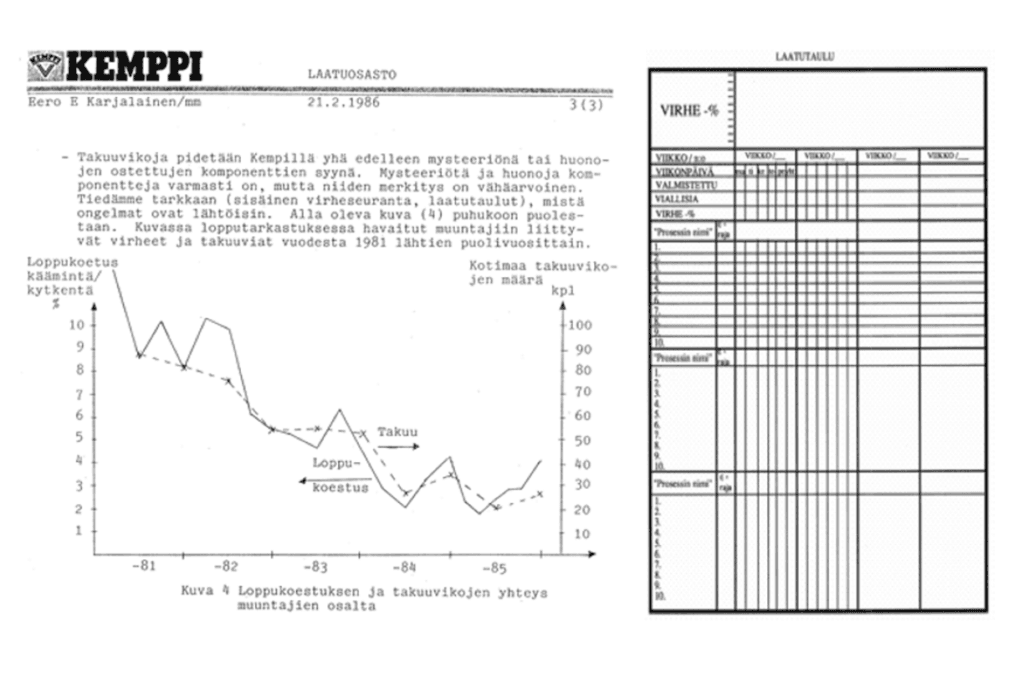
Kempillä virheet (”inputit”) kerättiin koko prosessista laatutauluilla ja niihin liittyvillä menettelyillä pyrittiin hävittämään viat paljastamalla virheet. Kun virheet inputeista häviää, siitä seuraa, että viat ja reklamaatiot outputeista häviävät.
Maksimissaan virheitä ilmoitettiin ja kerättiin noin 500 000 kpl/vuosi. Takuuviat (reklamaatiot) alenivat 5 vuodessa yli 90 %. Takuuviat olivat ja ovat seurausta sisäisistä virheistä. Niille ei ole mahdollista löytää yksilöllistä syytä lähtien takuun ”oireista”, reklamaatioista ja korjausilmoituksista, outputista. Vaikka syy löydettäisiin, ollaan 1-2 vuotta myöhässä.
c) Laatutaulu ja informaatio
Laatutaulumenettelyihin kuului työntekijöiden informointi ja koulutus.
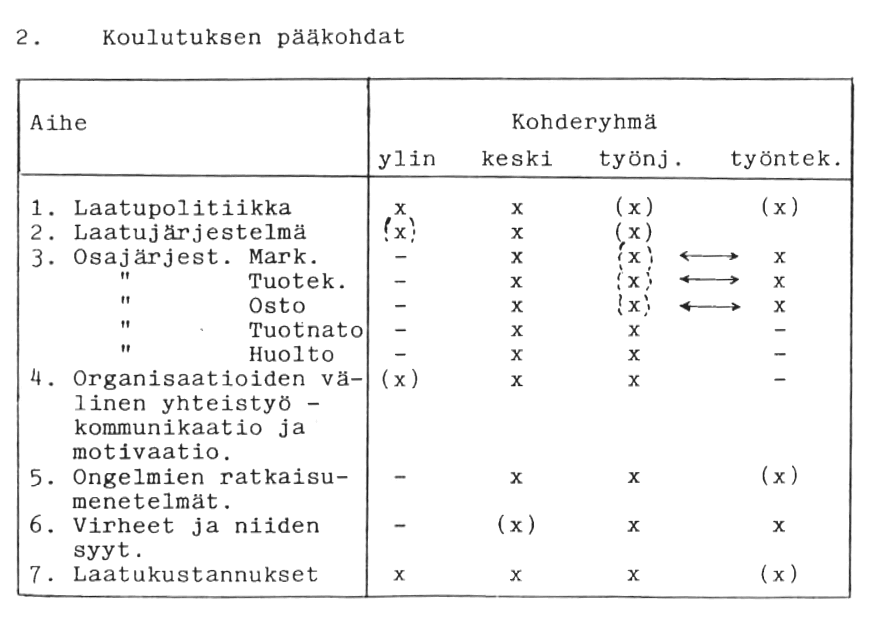
Vähintään kaksi kertaa vuodessa kaikki työntekijät (n. 400) koottiin työnjohtajittain laatuinfotilaisuuteen. Tilaisuuksien perusrunko oli aina sama:
- Sisäiset virheet (yhteenvetokäyrät laatutauluista)
- Ulkoiset virheet (takuu käyrät, koska johtuvat sisäisistä virheistä)
- Osastokohtaiset (työnjohtoalue) kehityskohteet ja projektit
- 1-2 ”uutta” koulutettavaa laatuasiaa, menetelmää
- Laatupiirit, laatukortit
- vialliset osat, 0-virhe-periaate
Tilaisuudet kestivät noin 1-1,5 h/kerta ja ryhmä. Ryhmiä 20-25 kpl.
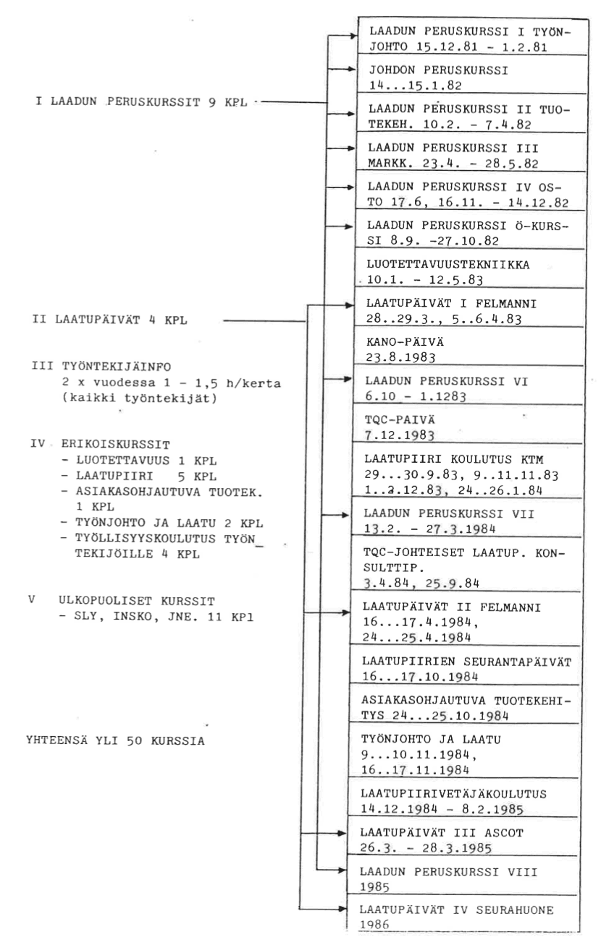
Yrityksessä pidettiin yli 50 sisäistä laatukoulutus ja tiedotustilaisuutta työntekijästä toimitusjohtajaan. Jokaisen toimihenkilön oli osallistuttava vähintään viiteen koulutustilaisuuteen (laadun perusteet, luotettavuustekniikka, ongelmanratkaisu, laatupiiri, QFD jne.).
Laatutauluja ja niihin perustuvaa laatujärjestelmää kehitettiin jatkuvasti. Taulut saivat uusia muotoja ja sovelluksia. Saavutuksesta Kemppi Oy sai Suomen Laatuyhdistyksen laatupalkinnon vuonna 1986.
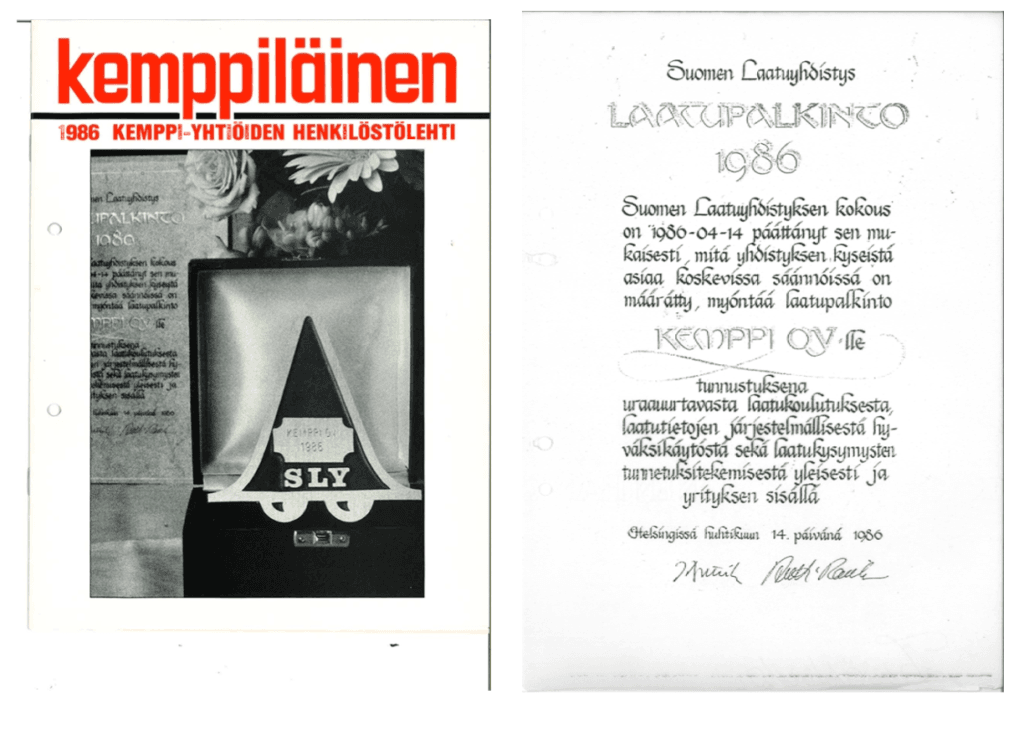
2. Yhteenveto
Laatutaulu edustaa murrosta, jossa siirrytään tarkastus- ja valvontaperusteisesta laatujärjestelmästä jatkuvan parantamisen ja ennaltaehkäisyn laatujärjestelmään. Tämä on täysin sopusoinnussa samoihin aikoihin syntyneen ISO 9000 -laatujärjestelmän kanssa.
Lähteet:
- Walter A. Shewhart: Economic Control Of Quality Of Manufactured Product, 1931
- W. E. Deming: The New Economics, 1992
- Artikkeli: Laatutaulu: virheet ja hukka – teoriasta käytäntöön: Osa 1, 2024
- Artikkeli: Jatkuvasta tarkastuksesta ja korjauksesta jatkuvaan parantamiseen tai sitten ei?, 2021
- Artikkeli: Prosessin ja työkoneen säätäminen ja asettaminen – OSA III, 2017
- Eero E. Karjalainen, Tanja Karjalainen: Laatutaulu – Tehokas menetelmä laadunohjaukseen ja paranukseen, 2024
- https://www.dqsglobal.com/fi-fi/opi/blogi/iso-9001-n-historia-menestystarina
- https://committee.iso.org/sites/tc176/home/news/content-left-area/news-and-updates/update-revision-of-iso-9001.html
- Artikkeli: Hyväksymisnäytteenotto, 2015
- Eero E. Karjalainen, Tanja Karjalainen: Lean Six Sigma 2.0 ja laatuteknologia, 2020
- Lauri Saari: VALCOinen kirja. 1981
- Pasi Nevalainen: Epäonnistumisen anatomia – Kuvaputkitehdas Valcon nousu ja tuho 1976-1980, Suomalaisen Kirjallisuuden Seura, 2022
- J. M. Juran: Quality Control Handbook, Third Edition, 1974
Tutustu kurssitarjontaamme!
Tilaa uutiskirje
Liity postituslistalle ja saat uusimmat artikkelit suoraan sähköpostiisi.
Tämä lomake on suojattu Google reCAPTCHA:lla. Lue tietosuojaseloste ja käyttöehdot.
Liittymällä postituslistalle hyväksyt Quality Knowhow Karjalainen Oy:n tietosuojaselosteen ja Quality Knowhow Karjalainen Oy voi lähettää sinulle ajankohtaisia artikkeleita, videoita sekä tietoa ja tarjouksia kursseista, kirjoista sekä ohjelmistoista.
Tämä lomake on suojattu Google reCAPTCHA:lla. Lue tietosuojaseloste ja käyttöehdot.