Vain 2 % lean-projekteista saavutti asetetut tavoitteet
Toyotaa on ylistetty ja ihailtu niin autoista kuin johtamistavasta. Eikä syyttä. Yritys on noussut autonvalmistajien kärkeen, kunnes pari vuotta sitten tuli ”takapakkia”. Toyotan autot käyttäytyivät (kiihtyivät) ennakoimattomasti. Epäiltiin polttoainesyöttöä ohjaavan elektroniikan piilevää vikaa. Toyota käynnisti autojen massiivisen takaisinvedon ja tutkimukset käynnistyivät.
Lean ja soveltamisongelmat
Takaisinvedon aikaan Lean koki myös vakavan syytöksen ja epäilyn. Onko Lean todella toimiva järjestelmä? Toyotahan tunnetaan hyvästä laadusta. Mielikuvaa vahvisti suuri kyselytutkimus, jonka suoritti Industrial Week/1/ (2008). Siinä havaittiin, että USA:ssa vain 2 % yrityksistä saavutti odotetut Lean tulokset. Onko Suomessa tilanne samankaltainen? Vaikutelma on, että näin olisi. Mitään tutkimusta tai haastattelua ei ole tehty, mutta asia on syytä ottaa esille. Voisimmeko oppia tästä jotain. Mitkä syyt voisivat olla epäonnistumisen takana. Onko syynä itse Lean ja Toyota vai Leanin ”virheellinen” soveltaminen?
Toyota ja USA:n autojen takaisinveto
Toyotan polttoaineen syötön/elektroniikan ongelma on nyt virallisesti ratkaistu/2/. 30 NASAn tutkijaa eivät kymmenen kuukautta kestäneissä tutkimuksissa löytänyt mitään elektroniikka tai kaasuttimeen liittyvää vikaa, joka olisi aiheuttanut auton nopeuden ennakoimattoman kiihtymisen. Sen sijaan ongelman syyksi on varmistumassa lattiamatto, joka on ainakin kahdessa tapauksessa aiheuttanut ongelman. (”Sticking” accelerator padals and a design flaw that enablend accelerator pedals to become trapped by floor mats. These are the only causes for the raported unintended acceleration incidents.”). Toyota ei ole kiistänyt maton mahdollista syytä.USA:n ja myös Suomen media antoi ongelmasta kuvan, että takaisinveto ja korjaus olivat ennätyksellisen suuria. Todellisuudessa takaisinveto oli ”tavanomainen” ja taisikin olla niin, että ainakin osittain oli kysymys antimarkkinoinnista. Kuvassa on USA:n autovalmistajien 10 suurinta takaisinvetoa ja ”lattiamatto” on viides/3/. Elektroniikan takaisinveto (2,2 milj.) ei edes pääse listalle.
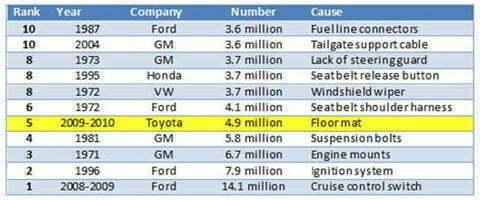
Lean ja soveltamisen ongelma
Toyota liitetään autoihin, mutta myös Leaniin. Toyota ja Lean ”selvisivät” ainakin tällä kertaa testistä. Uskokaamme Leaniin ja hakekaamme syytä Leanin projektien epätyydyttävään onnistumiseen Leanin soveltamisesta!
Industrial Weekin tutkimuksen lisäksi lukuisissa muissakin yhteyksissä on esitetty, että Leanin soveltaminen epäonnistuu 70-90 %:ssa tai jopa enemmän/4,5/. Vielä vakavampaa on, että arvostettuja Shingo Prize palkintokriteereitä on jouduttu muuttamaan/8/. Palkitut Leanin malliyritykset (best practice) viimeisten 20 vuoden aikana eivät pystyneet ylläpitämään tuloksia. Syynä on keskittyminen Lean työkaluihin, ei Lean kulttuuriin. (”We studied those companies and found that a very large percentage of those we had evaluated, were experts at implementing tools of lean but had not deeply embedded them into their culture”: Robert Miller, Executive Director Shigoe Prize, 2010)
Lean on edelleen ”uusi” tuotannon paradigma, joka muuttaa perusteellisesti tapaa tuottaa palveluja ja tuotteita. Kirjat ”The Machine That Changed the Word”/6/ ja ”Lean Thinking”/7/ loivat Lean käsitteen1990 luvulla. Siirryttiin ammattityöstä massa-tuotantoon. Leanissa fokus on asiakkaassa ja arvovirrassa. Leanin voi kuvata myös pyrkimyksenä täydellisyyteen, joka toteutetaan eliminoimalla jatkuvasti hävikkiä ongelmanratkaisun avulla (huom. ei Lean työkalujen avulla). Hävikkiä ja parantamisen varaa meillä totisesti on – vain alle 1 % palvelun ja tuotteen läpimenoajasta lisää sen asiakasarvoa. Jos tätäkään asiaa, asiakasarvoa, ei ole ymmärretty niin vielä vähemmän ymmärretään Leanin keskeistä parannusmenetelmää ongelmanratkaisua ja sen avainasemaa (problem solving). Ongelmanratkaisun tärkeyden vuoksi Lean ja Six Sigma on yhdistetty Lean Six Sigmaksi. Toyotan käyttämistä ongelmanratkaisumenetelmistä ei ole vastaavaa julkista tietoa kuin Six Sigmasta. Vain erityissyiden osalta tunnetaan Toyotalta A3. Viitteet Toyotan menetelmän ja Six Sigman samankaltaisuudesta ovat ilmeiset. Molemmat perustuvat samaan Demingin ketjureaktioon ja PDCA:aan.
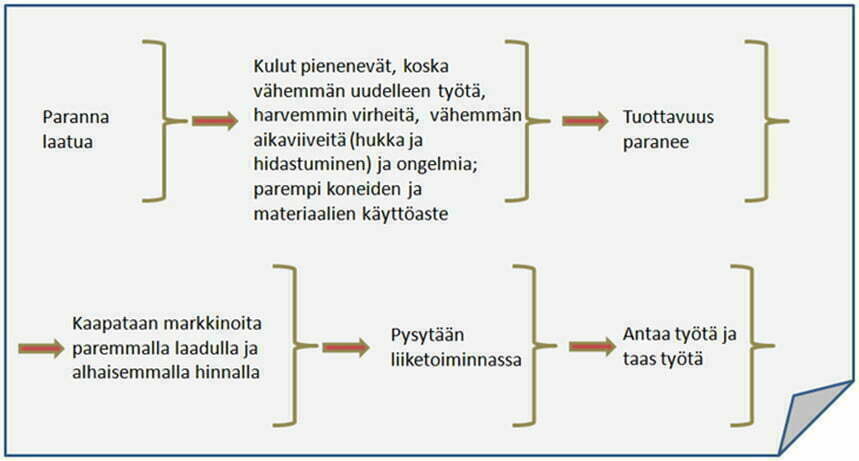
Mistä parannus tulee
Tutkittaessa Toyotan tehtaita havaitaan, että Toyotan yksiköissä on TPS (Toyota Production System) osasto ja insinöörit, jotka suunnittelevat Lean innovaatiot (näin kirjoittavat Jeffery Liker ja Mike Rother/8/). Soveltavatko nämä Lean Expertit ensisijassa standardoituja Lean työkaluja (5S, kanban, heijunka, SMED, ANDON jne)? Eivät. Sen sijaan tehtaissa sovelletaan Lean ilmapiiriä, kulttuuria, tilaa, jossa tehdään lukuisia pieniä parannusyrityksiä joista jotkut onnistuvat ja jotkut eivät. Kysymys on tieteellisestä ongelmanratkaisusta Plan-Do-Chek-Action (PDCA), korostan tieteellisestä ongelmanratkaisusta, Leanin toisesta komponentista. Lean-työkaluilla on kaksinainen rooli, näkyvä ja näkymätön. Ne auttavat vähän Leanin suuntaan, mutta ennen kaikkea ne viestivät ”näkymättömän” tavoitetilan, johon pyritään jatkuvalla tieteellisellä ongelmanratkaisulla. Näin Leanista tulee dynaaminen ja se pysyy vuodesta toiseen kilpailukykyisenä ja joustavana, vaikka olosuhteet muuttuvat.
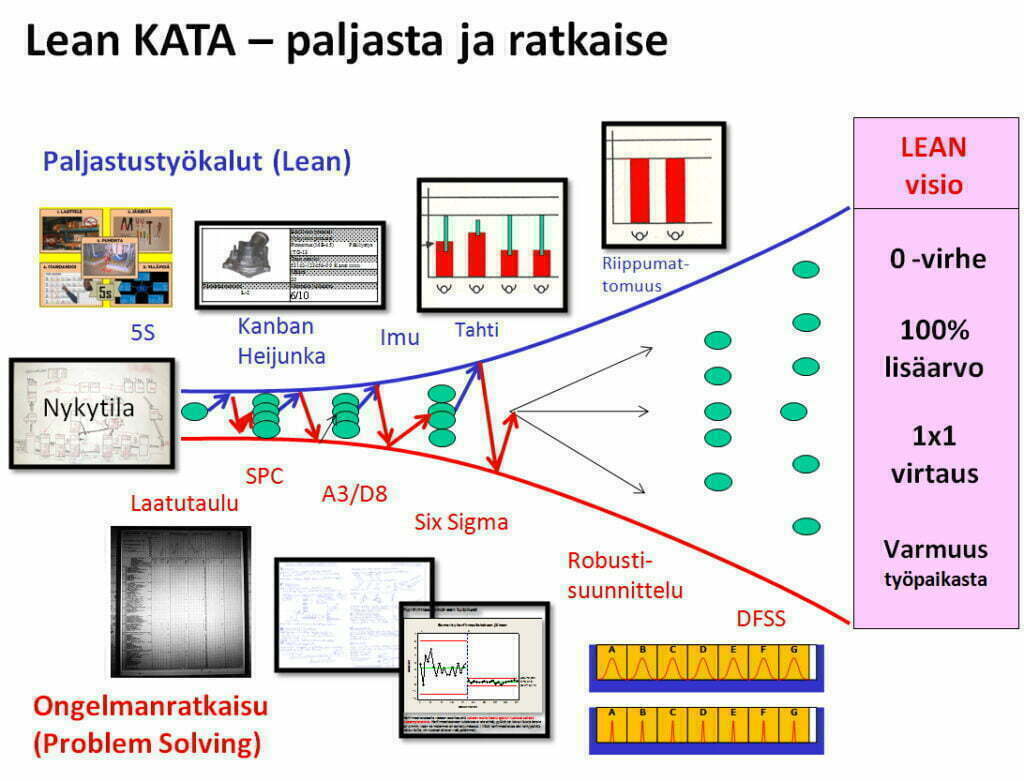
Mike Rother on tutkinut vuosikausia Toyotaa ja sen menestyksen salaisuutta ja kuvannut tutkimuksen tulokset suomeksi ilmestyvässä kirjassa ”Toyota Kata – Ihmisten johtamista kohti parantamista, mukautumista ja parempia tuloksia”/9/. Kata on hyvin tutkittu parannusmenetelmä, rutiini, protokolla, tieteellinen ongelmanratkaisu, joka mahdollistaa onnistuneet parannukset. Olen artikkeleissa käsitellyt näitä rutiineja/10/. Sattumalta tai ei Toyotan kata, parannusrutiini muodostuu viidestä hyvin samankaltaisesta vaiheesta kuin mitä Six Sigman ”mousetrap” (DMAIC), kata.

Leanin ongelma
Olemme Suomessakin nähneet useassa yrityksessä Leanin soveltamisen keskeisen ongelman, joka liittyy ns. Lean työkaluihin ja niiden ”kevyeen” soveltamiseen. On syntynyt ”teolliset turistit”, ”best practise”-ihmiset, jotka etsivät käytännön esimerkkejä, kuinka Leania pitäisi soveltaa. Teollinen turismi alkoi, kun Italian Venetsiassa 1574 ensimmäisen kerran toteutui Lean perusteinen laivanrakennus/4/. Laiva valmistui liukuhihnalta 1-3 päivässä. Henry Fordhan toteutti tämän sitten 1900 luvun alussa ja Toyota nyt. Kaikki nämä ”tehtaat” – Venetsia, Ford, Toyota – ovat sallineet teolliset turistit tietäen, että kopiointi ei onnistu. Näemme vain pinnan, työkalut. Työkalut paljastavat parhaimmillaan hävikin ja polun kohti Leania, kuten artikkelissani ”Ymmärrä Lean ja Six Sigma oikein – Kymmenen harhaluuloa ja väärinymmärrystä”/10/ osoitin, mutta pelkän työkalun käyttö tuo tuskin havaittavaa hyötyä. Kysymys on ihmisen ja organisaation oppimisesta, joka on vaativa ja aikaa vievä prosessi, jonka on perustuttava tieteelliseen menettelyyn (PDCA tai DMAIC).
Lyhyillä Lean-kursseilla voi oppia Leanin ”työkalut”, mutta itse Lean ja sen kata jää usein hataraksi tai sitä ei opita ollenkaan. Samoin on laita Six Sigman osalta. Vasta noin kuukauden (20 päivää) Lean Leader tai Lean Six Sigma Black Belt koulutus luo riittävän pohjan ymmärtää ja sisäistää menetelmiä. Lisäksi tarvitaan vielä paljon harjoittelua – Lean sovellutus ja/tai Black Belt -projektityö tai useita töitä. Organisaatiossa myös johtamisen on tuettava parannusta.
Lean ja oppiminen
Uusimmat neuropsykologian tutkimukset ovat demonstroineet, että ihmiset kehittävät itselle sopivan neutraalin polun, joka mahdollistaa asioiden tekemisen mukavasti yhä uudelleen ja uudelleen. Kokouspaikalla hakeudumme aina samaan istumapaikkaan! Ihminen saa tästä turvallisuutta ja luottamusta, mutta sisältö ja olosuhde, jossa olemme, kuitenkin muuttuu, tahdomme tai ei. Vastalääke tähän muutoksen ”stressiin” ja luontaiseen pyrkimykseen vastustaa muutosta on kehittää vahvat mentaaliset mallit ratkaisujen kehittämiseen (so. ongelmanratkaisu, kata) ratkaisujen sijaan (so. työkalut).
Leanissa yritysjohdon on luotava parannuksen rutiinit – parannus KATA. Rutiini ratkaisuun on se puuttuva rengas, jolla Lean projektit ja ohjelmat saa onnistumaan paremmin. Tavoitteet ja työkalut kyllä on ja myös mittarit, mutta rutiini puuttuu. Rutiini, joka on riittävä viemään kohti tavoitetilaa, muuttuvat olosuhteet miksi tahansa.
Tutkimus on selkeästi osoittanut että, jos tehtävä on suhteellisen helppo – sen ”polku” kohti tavoitetta on tunnettu/tiedetty – silloin johtaminen tuloksilla, mittareilla ja ulkoisilla motivointikeinoilla voi toimia kohtuullisen hyvin. Tehtävä on tyyppiä ”tee se vain”. Johtajan ei tarvitse huolehtia, että tehtävä suoritetaan systemaattisesti, tieteellistä menettelyä noudattaen, jotta tavoite saavutetaan.
Toisaalta, jos tehtävä on haasteellinen – sen tie tavoitteeseen ei ole selvä ja polku on etsittävä iteratiivista oppimista hyväksi käyttäen – silloin johtaminen tuloksilla ja ulkoisilla porkkanoilla ja rangaistuksilla ei toimi hyvin. Tässä tapauksessa tärkeäksi muodostuu, kuinka työntekijä johdatetaan tavoitetilaan (tulokseen). Johtajan on huolehdittava tavoitteen lisäksi myös parannusmenettelystä, tieteellisestä menettelystä, katasta, jota noudattamalla ongelmien ratkaisu onnistuu. Jos ihminen pystyy ratkaisemaan ongelmia, motivaatio nousee. Johtajan keskeinen keino motivoida henkilöstöä on taata ongelmien ratkaisun onnistuminen. Motivaation lisäksi ihmiset tarvitsevat edelleen paljon koulutusta tieteelliseen ongelmanratkaisuun esim. PDCA, SPC, Six Sigma, 8D, A3, ATS, DFSS jne. Osaamisessa on luvattoman paljon aukkoja.
Kun Leania katsotaan tästä näkökulmasta, se on paljon enemmän kuin joukko Lean työkaluja, joilla hävikkiä voidaan paljastaa. Kyllä Toyotan Lean olisi kopioitu ja ”best practätty” ajat sitten. Lean on prosessi, jossa johtaja (lean leader) kehittää ja johtaa työntekijöitä niin, että tavoitetila saavutetaan yhä uudelleen ja uudelleen. Tämä tarkoittaa parannuksen menettelytavan (kata) toteuttamista yrityksessä joka päivä yhä uudelleen ja uudelleen.
Hanki yritykseesi riittävä tieto-taito ja muuta Leanin 2% onnistumisen todennäköisyys 85-95%:iin. Tätä edesauttaa esim. Lean Leader tai Lean Six Sigma Black Belt, jotka osaavat niin näkyvät kuin näkymättömätkin Lean ja ongelmanratkaisuperiaatteet, käytännöt ja työkalut ja joilla on ohjattu ja todistettu kyky (sertifikaatti) toteuttaa Lean ja/tai Lean Six Sigma projekti/ohjelma. Aloita vasta sitten Lean.
Lähteet:
1. Everybody´s Jumping on the Lean Bangowagon, but Many are Being Taken for a Ride. Industry Week, May1, 2008
2. www.nasa.gov/topics/nasalife/features/nesc-toyota-study.html
3. www.rpmgo.com/11-biggest-auto-recalls-inhistory
4. James P. Ignizio: Optimizing Factory Performance – Cost Effective Ways to Achive Significant and Sustainable Improvement, 2009
5. Wallace J. Hopp, Mark L. Spearman: Factory Pysics, Third edition 2008
6. J. Womack: The Machine That Changed the Word, 1990
7. J. Womack: Lean Thinking, 1996
8. Jeffery Liker, Mike Rother: ”Why Lean Program Fail” LEI, 2011
9. Mike Rother: Toyota KATA (suomennettu) 2011 (Englanninkielinen alkuperäisteos: Toyota Kata 2010)
10. Eero E. Karjalainen: ”Ymmärrä Lean ja Six Sigma oikein – Leanin kymmenen harhaluuloa ja väärinymmärrystä”, 2010
Tilaa uutiskirje
Liity postituslistalle ja saat uusimmat artikkelit suoraan sähköpostiisi.
Tämä lomake on suojattu Google reCAPTCHA:lla. Lue tietosuojaseloste ja käyttöehdot.
Liittymällä postituslistalle hyväksyt Quality Knowhow Karjalainen Oy:n tietosuojaselosteen ja Quality Knowhow Karjalainen Oy voi lähettää sinulle ajankohtaisia artikkeleita, videoita sekä tietoa ja tarjouksia kursseista, kirjoista sekä ohjelmistoista.
Tämä lomake on suojattu Google reCAPTCHA:lla. Lue tietosuojaseloste ja käyttöehdot.