Erinomainen laatu palveluissa ja tuotteissa takaa kestävät taloudelliset tulokset, koska palvelut ja tuotteet, jotka ovat erinomaisia kilpailijoihin nähden myyvät enemmän ja niiden tuottaminen on halvempaa ja nopeampaa. Palvelut ja tuotteet, jotka ovat laadullisesti myyvempiä ja menestyneempiä vaikuttavat vahvasti liikevaihtoon ja samalla omaavat alhaisemmat kustannukset, joka taas johtaa suurempaan voittoon. Erinomaista laatua tavoittelemalla ja haastamalla yrityksen sisäiset toiminnat voi muuttaa yrityksen ja sen kulttuurin ja toimintatavat, kuten Toyota tai Kone Oyj tekivät. (Matti Alahuhta ”Johtajuus – kirkas suunta ja ihmisten voima”/1/)
Mitä laatu maksaa?
Usein laadusta keskusteltaessa nousee kaksi vastakkaista kysymystä:
- Eikö korkea laatu maksa enemmän?
- Eikö korkea laatu maksa vähemmän?
Puolet vastaajista on sitä mieltä, että laatu maksaa enemmän ja puolet, että laatu maksaa vähemmän. Mistä tämä epämääräisyys? Sama sana LAATU merkitsee kahta eri asiaa – 1. asiakkaalle luvattua ominaispiirrettä, ominaisuutta ja 2. asiakkaalle luvatun ominaispiirteen puutetta, virheettömyyttä. Sama sana LAATU ja kaksi täysin vastakkaista näkökulmaa – ”hyvyys” ja ”pahuus”.
Tarkastellaan tilannetta seuraavan kuvan avulla/2/, mitä korkeampi laatu mahdollistaa organisaatiolle.

Edellä olevan ”laatuongelman” ratkaisemiseksi moniselitteinen LAATU-sana on laatujohtamisessa ja teknologiassa korvattu yksiselitteisellä asiakaslähtöisellä sanayhdistelmällä ”sopivuus käyttöön” (J. M. Juran) tai ”vaatimusten mukaisuus” (W. E. Deming) tai vielä yleisemmin ”tuotteen ja palvelun kyky täyttää asiakasvaatimukset”. Näin laatuun on saatu yksi ”valuutta”, yksi yhteinen nimittäjä, jonka mittarina toimivat asiakastyytyväisyys ja lojaalisuus. Lojaalisuus kuvaa pitkäaikaista tyytyväisyyttä ja sitoutumista.
Asiakastyytyväisyys ja lojaalisuus voidaan saavuttaa vain kun molemmat laadun dimensiot, ominaispiirteet ja virheettömyys, on saavutettu tehokkaalla johtamisella. Matti Alahuhta, Kone Oyj, nimeää nämä keskeisiksi mittareiksi/1/. ”Laadun lähtökohta on aina asiakkaan ääni. Laadun kehittämisessä on pohjimmiltaan kyse asiakastyytyväisyyttä lisäävän toiminnan kehittämisestä. Asiakastyytyväisyyttä pystyy parantamaan ymmärtämällä, mikä yrityksen toiminnassa estää luomasta lisäarvoa asiakkaalle.”
Ominaispiirteiden kehittäminen – Laadun suunnittelu
Esittelin edellisessä artikkelissa: Asiakaslähtöinen tuotekehitys (QFD)/3/ asiakkaiden tarpeiden tunnistamista ja näiden tarpeiden perusteella luotavia palvelu- ja tuoteominaispiirteitä eli kansanomaisemmin ”speksejä, toimintatapoja”, jotka takaavat kuvan 1 mukaiset kustannusedut organisaatiolle ja samalla myynnin kasvun. Laatu maksaa, mutta jos asiakas on halukas maksamaan kustannuksia enemmän, on laatu hintansa väärti!
Laadun parannus ja sen mahdollisuus
Laadun toinen puoli on virheet, jotka vaikuttavat voimakkaasti sekä yrityksen tuloihin että kustannuksiin. Asiakas ei osta palvelua tai tuotetta tai syntyy lisäkustannuksia, tuotepalautuksia, reklamaatioita, uusintatyötä jne. Näitä kustannuksia kutsutaan huonon laadun kustannuksiksi (COPQ, Cost of Poor Quality). Laatukustannusten laskenta voi olla yritykselle erinomaisen tärkeää ja samalla liikkeenjohdolle keino haastaa yritys parannuksen tielle.
Palveluorganisaatioiden laatukustannukset ovat erittäin korkeat. Noin 30-35 % liikevaihdosta/2/. Luku sisältää uudelleen tekemisen, ylimääräiset huonon laadun ohjauskustannukset ja kustannukset, joilla tyydytetään ”hukattu” asiakastarve.
1980-luvulla teollisuuden laatukustannukset olivat 20-25 % liikevaihdosta/2/. Vuonna 2003 arvioitiin laatukustannusten olevan vielä 15-20 % liikevaihdosta. Noin 5 % yksikön parannus on ilmeisesti seurausta 1990-luvulla yleistyneestä Six Sigmasta. Korkeita lukuja molemmat. Nämä luvut ovat usein täysin tuntemattomat yrityksen sisällä. Tästä seuraa, että yritysjohto ei osaa tai halua ”haastaa” ja organisoida yritystä sekä sen johtajia ja päälliköitä parantamaan toimintaa – Matti Alahuhdan termiä käyttääkseni!
Seuraavassa tyypillisiä palveluongelmia, jotka on verrattavissa vastaaviin tuoteongelmiin. Nämä ja monet muut luovat huikean potentiaalin yritysjohdolle, mutta niitä on pystyttävä haastamaan ja parantamaan. On saatava aikaan toimintaa. Kuva 2 on luotu 8 hukkaluokittelun perusteella.

Kuinka parannetaan – Lean Six Sigma
Yksi keskeisistä parannusmenetelmistä palvelu- ja teollisuustuotannossa on Lean ja Six Sigma. Six Sigma on jopa standardoitu menetelmä ja näin virallinen EU-normi: ISO 13053:1 ja 2 ”Prosessin kehittämisen kvantitatiiviset menetelmät. Six Sigma. Osa 1: DMAIC-menetelmä ja Osa 2: Työkalut ja tekniikat”. Standardin saa suomeksi SFS:ltä. Suosittelen. (P.S. Kääntäjälle on tullut virhe –> improvement käännetty kehittämiseksi vaikka kyseessä on parannus).
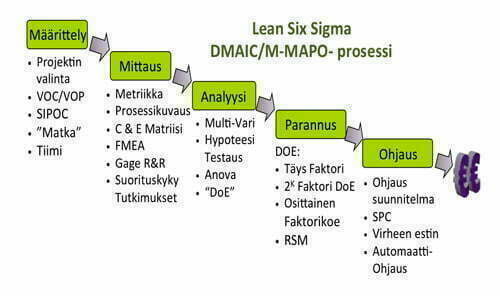
Yhdistettynä Lean ja Six Sigma muodostavat tehokkaan liikkeenjohdon parannusmenetelmän:
- Lean keskittyy lisäämään prosessin vuota (ulostulosuhde = kuinka monta tuotetta tai palvelua valmistuu esim. päivän aikana kpl/päivä), lyhentämään jaksoaikaa ja eliminoimaan hukkaa prosessissa.
Huomaa, että kun prosessin vuo paranee, siis kasvaa, samanaikaisesti jaksoaika kasvaa. Littlen laki CT=WIP/TH! Tarvitaan erityistä optimointia ristiriidan ratkaisemiseksi. Vastaavasti pelkkä läpimenoajan lyhentäminen laskee valmistuvien suhdetta ja heikentää yrityksen kannattavuutta. - Six Sigma keskittyy tunnistamaan ja poistamaan vikojen syyt ja minimoimaan vaihtelua prosessissa.
Sekä Leanin että Six Sigman perustavaa laatua oleva juurisyy ja perusongelma on vaihtelu, variation, jota mitataan hajonnan keskiarvolla eli sigmalla.
- Lean: Jos eri työvaiheiden kestoissa tai palvelukysynnässä ei olisi aikavaihtelua töiden ja työvaiheiden välillä ja kesken: joka minuutilleen tulisi aina sama määrä asiakkaita, työ- ja palveluajat eivät vaihtelisi, meillä ei olisi aikahukkaa, waste. Hukka ja pitkät läpimenoajat syntyvät aika/nopeuserovaihtelusta (jonoutuminen, queuing). Myöskin palvelu tai tuotantoyksikön kapasiteetti olisi helposti säädettävissä 100 %:iin, kun se nyt on 0,1-5 %. 95 % – 99,9 % ajasta on odottamista jonoissa!
- Six Sigma: Jos mikään materiaali, sen ominaisuus ei vaihtelisi tai heikkenisi/muuttuisi, meillä ei olisi virheitä, puutteita, loss. Kaikki olisi täydellistä. Meillä olisi 0-virhettä. Nyt virheitä on 30-50 % tai jopa enemmän tuotettua yksikköä ja mahdollisuutta kohden. Six Sigman tavoite on 0,0000034 % eli 3,4 ppmo.
Vaihtelu on kuitenkin luonnon laki! Sitä on aina ja kaikkialla, mutta onneksi sitä vastaan voidaan ”taistella” eli parantaa palvelun ja tuotteiden suorituskykyä ja samalla voimme parantaa merkittävästi myös liiketoimintaa – potentiaalia on vähintään kolmasosa liikevaihdosta! On vain osattava haastaa tämä mahdollisuus.
Ongelmanratkaisun polun valinta
Oikean ja tehokkaan ongelmanratkaisupolun valinta on haasteellista. Yhtä haasteellista kuin lääkärillä saada oikea diagnoosi. Onneksi meillä on ”samat ” työkalut laadun parantamisessa kuin ”ihmisvirheissä”. Kvalitatiivisen lääkärin haastattelun eli oirekuvausten lisäksi voidaan käyttää mittauksia. Numerot ovat numeroita, mutta jos niihin liitetään tyypillisiä arvoja kuvaavat rajat, viitearvot, on analyysi helppoa vrt. Laboratoriokokeiden viitearvot (kuva 4).
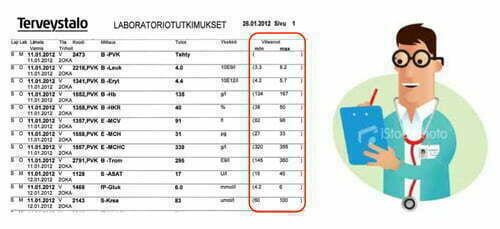
Jos analyysi poikkeaa viitearvosta, tyypillisistä ihmisten arvoista, on kyse ehkä akuutista sairaudesta, johon todennäköisesti löytyy lääke, jos ei, on ongelma vaikea ja monimutkainen, suorituskykyyn liittyvä krooninen ”terveys”. Tämän saman informaation tarjoaa SPC (Statistical Process Control) ja softat esim. Minitab. Tämän avulla voi suunnistaa oikean ratkaisumenetelmän, diagnoosin, valintaan./4/
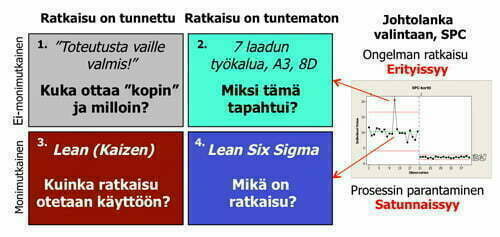
- Jos on kyse erityissyystä (piste ohjausrajan ulkopuolella, poikkeaa ”viitearvoalueelta”, akuutti sairaus) ja ratkaisu tiedetään, ongelma on toteutusta vaille valmis. Kysymys on: Kuka ottaa kopin ja milloin?
- Jos ei ratkaisua tunneta, on käytettävä 7 laadun perustyökalua, A3, 8D, PDCA tai muita ongelmanratkaisumenetelmiä ja tiimiä laajentamaan näkemystä ja ideoimaan ratkaisuehdotuksia.
- Jos ongelmana on suorituskyky (≈ krooninen sairaus, terveys). Prosessin arvot ovat ohjausrajojen sisällä ja prosessin suorituskyky ei riitä vaatimuksiin, on tilanne haastava. On käytettävä joko ”valmiita” Lean -ratkaisuja. Tällöin on hyvin huolellisesti selvitettävä, sopiiko ratkaisu – Kanban, imuohjaus, SMED, 5S, solutuotanto tai jokin muu Lean -menetelmä juuri minun yritykseeni. Onko yritykseni imitoidun tai kopioidun yrityksen kaltainen, jossa menetelmää on käytetty ja mitkä ovat olleet tämän yrityksen tulokset. Lean on kuin ostaisi verkkokaupasta vaatteen, jota ei voi sovittaa eikä palauttaa! Hyvä, nopea ja halpa menetelmä, jos ratkaisu sopii. Vaatii kuitenkin erillisprojektin esim. VSM – Lean Leader.
- Lean Six Sigma -menetelmässä ei ole olemassa yksinkertaista ratkaisua, ongelma on monimutkainen, kuten lähes kaikki liikkeenjohdon ongelmat. Lean Six Sigmassa haetaan juurisyy, johon tehdään sopivaksi katsottu muutos, joka saa aikaan parannuksen, joka testataan ennen käyttöönottoa. Valittu muutos voi olla tai sitten ei Leanin tarjoama ratkaisu, mutta se on sovitettava juuri tähän tapaukseen. Lean Six Sigmassa ei ”osteta” mitään menetelmää ilman sovittamista, koetta DoE. Lean Six Sigma vaatii erillisen Black Beltin tai vaihtoehtoisesti Green Beltin johtaman projektin.
Lähestymistapaa valittaessa on hyvä muistaa vanha ja viisas sanonta, jonka Sixten Korkman esittää kirjassaan ”Väärää talouspolitiikkaa”/5/:
Jokaiseen vaikeaan ongelmaan on tarjolla ratkaisu, joka on yksinkertainen, houkutteleva – ja väärä.
Älä valitse väärää ratkaisua. Siispä käytä SPC:tä. Hyvä järjestys harkita toimenpiteitä on SPC plus 4, 3 ja 2, 1!
Ongelmanratkaisukoulutus
Kaikki menetelmät vaativat jonkin asteisen koulutuksen, osaamisen ja ammattitaidon.
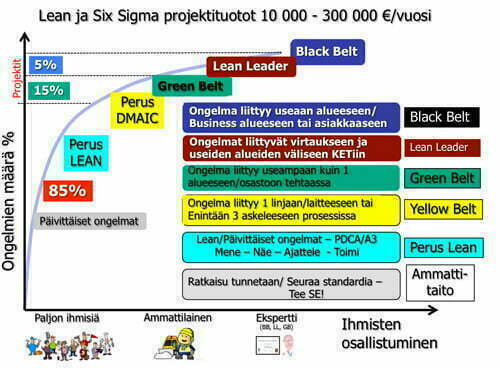
Organisaatiossa suuri osa (85 %) ongelmista on ”Toteutusta vaille valmiit”. Nämä voidaan tunnistaa SPC:n, laatutaulujen, avulla tai ammattitaidolla ja ratkaista yksinkertaisin menetelmin. Jos nämä ”epästabiilisuus” ongelmat jäävät ratkaisematta, ne ajan myötä muuttuvat suorituskykyongelmiksi. Jos talon kattoon tulee reikä, sen korjaamatta jättäminen muuttaa koko talon hometaloksi tai kouluksi, todelliseksi suorituskykyongelmaksi! Suositeltavaa on käyttää SPC:tä ohjaamaan välittömiin toimenpiteisiin kuin pelkkää johtamista tai ammattitaitoa. Ihminen sokeutuu virheille, aliarvioi niiden määrän karkeasti eikä halua haastaa niitä!
Yrityksessä tai organisaatiossa on muutamia kymmeniä todella vaativia ongelmia, jotka sanelevat lähes koko organisaation hyvinvoinnin ja tuloksenteon – suorituskykyongelmia. Näiden Lean ja Six Sigma parannusten kustannusvaikutus yrityksen tulokseen on määräävä (80-95 %). Toyotasta professori Konichi Shimizu on todennut, että 90 % parannuksista tekee insinöörit ja 10 % työntekijät (Toyota KATA 2004, s. 128).
Näiden vakavien suorituskykyongelmien alla olevat prosessit on asetettava ”mikroskoopin” alle ja tehtävä perustavaa laatua oleva analyysi ja muutoksia prosessiin. Ne vaativat aina projektin ja hyvin strukturoidun menetelmän, DMAIC. Tämä menetelmä ja työkalut on kuvattu ISO 13053 -standardissa.
Lähteet:
- Matti Alahuhta: Johtajuus –kirkas suunta ja ihmisten voima, 2015
- Joseph DeFeo, J. M. Juran: Juran’s Quality Essential, 2014
- Artikkeli: Asiakaslähtöinen tuotekehitys (QDF)
- The Global State of Quality, ASQ, 2013
- Roger W. Hoerl, Ronald D. Snee: On Size Does Not Fit All, Quality Progress, May, 2013
- Sixten Korkman: Väärää Talouspolitiikkaa, 2015
Tilaa uutiskirje
Liity postituslistalle ja saat uusimmat artikkelit suoraan sähköpostiisi.
Tämä lomake on suojattu Google reCAPTCHA:lla. Lue tietosuojaseloste ja käyttöehdot.
Liittymällä postituslistalle hyväksyt Quality Knowhow Karjalainen Oy:n tietosuojaselosteen ja Quality Knowhow Karjalainen Oy voi lähettää sinulle ajankohtaisia artikkeleita, videoita sekä tietoa ja tarjouksia kursseista, kirjoista sekä ohjelmistoista.
Tämä lomake on suojattu Google reCAPTCHA:lla. Lue tietosuojaseloste ja käyttöehdot.