Lean ja Six Sigma liittyvät pitkään laatumenetelmien ketjuun, jolla on kivetty modernin teollisen ajan laatuteknologian valtatietä 1700-luvun lopusta lähtien. Erilaisten laatu- ja tuottavuusmenetelmien syntyä on aina edeltänyt jokin merkittävä tuotteisiin ja palveluihin tai niiden toteuttamiseen liittynyt murros tai epäonnistuminen. Näistä murroksista voimme oppia edelleen uutta ja yllättävää.
Laadun kokonaiskuva
Uudessa kirjassamme Lean Six Sigma 2.0 ja Laatuteknologia (julkaistu 12.10.2020) pyrimme luomaan kokonaiskuvaa laadun toteuttamisesta ja sen vaikutuksista liiketoiminnan tuloksiin Lean Six Sigma -viitekehyksen kautta. Ei riitä, että yrityksessä keskitytään Leaniin ja Six Sigmaan. On hyvä hakea osaamisen ja kyvykkyyden tasapainoa kaikkien yritykselle tärkeiden laatuun ja tuottavuuteen vaikuttavien tekijöiden osalta. Se mitä historiasta on opittu, on edelleen tärkeää ja käyttökelpoista. Lean Six Sigma luo uuden täydentävän ja korjaavan kerroksen laadun valtatiehen.
Lähes kaikki yritykset, joita on kohdannut jokin odottamaton tuloksen heikkeneminen tai menestymättömyys markkinoilla, ovat törmänneet erilaisiin näkyviin tai näkymättömiin ja tiedostamattomiin vaihtelun aiheuttamiin laatu- ja tuottavuusongelmiin (ominaisuus- tai aikaväliongelmiin).
Tuotteet ja palvelut eivät vastaa valitun segmentin tarpeisiin, ne eivät kestä markkinoilla, tuotanto- ja palvelukustannukset ovat epästabiilisuudesta ja suorituskykypuutteista johtuen liian korkeat, aikataulut pettävät, laadunohjaus pettää tai toteutetaan virheellisillä menetelmillä, lopputarkastus vuotaa, reklamaatioiden tutkimus ja reagointi lisäävät reklamaatioita jne. Lista on loputon, mutta onneksi hallittavien ja osattavien menetelmien määrä on rajallinen. On vain muutama keskeinen periaate ja teknologia, joilla ongelmat saadaan vähenemään tai jopa kokonaan poistettua. Tri J. M. Juranin laadun trilogiassa on vain kolme keskeistä konseptia: laadun suunnittelu, laadun ohjaus ja laadun parantaminen. Näille kullekin oma prosessinsa. Laatuteknologiaa toteuttavia laatutekniikoita ja työkaluja on kuitenkin 300-400 kpl, joista on osattava valita oikeat, mutta ongelma on aina tunnistettava ennen työkalujen valintaa.
Modernin laatuteknologian kehityskaari – opiksi otettavaa
Teollisen ajan laatuteknologian alku liitetään usein USA:n varustautumisena maassa käytäviin sotiin ja keksijä Eli Whitney saamaan suureen 10 000 musketin (kiväärin) tilaukseen 1798 U.S. hallitukselta. Keksijä Eli Whitney lupasi toimittaa tilauksen kahdessa vuodessa ja niin, että muskettien osat olivat vaihdettavia. Vaihdettavuus oli ja on erittäin tärkeää. Se mahdollisti osien tekemisen irrallisena ja eri aikaan itse tuotteesta. Tuotteen ja osan välinen keskinäisvaikutus oli purettu valmistusvaiheessa!
Eli Whitney ei kuitenkaan pystynyt tuottamaan tarvittavia ”yhteensopivia” osia eksaktilla ”ajattelulla” – kaikista erilaisista osista tehdä itsensä kanssa samanlaisia. 10 000 muskettiin tarvittiin n. 0,5 milj. osaa (50 erilaista osaa/musketti). Toimitusaika (tilauksen jaksoaika) venyi sovitusta 2 vuodesta 9 vuoteen ja täysin vaihdettavien osien osalta 25 vuoteen! Toimitusongelman syynä oli osien yhteensopimattomuus, josta seurasi tuottavuus- ja toimitusaikaongelma! Eikö kuulosta tutulta tänäkin päivänä?
Eli Whitney joutui luomaan ja kehittämään mittaus- ja tarkastustoimintaa (rako-, reikä- ja muita tulkkeja ja jigejä), jotta muskettien valmistus onnistui vaihdettavista osista. Tästä prosessista sai alkunsa uusi toleransseihin ja tarkastukseen ja ”korjaukseen” perustuva tuotantomenetelmä – 1840 keksittiin GO testaus osille ja 1870 NOGO (ja laatutekniikka, toleranssit). Olen nimittänyt tätä kahden reiän koetusopiksi! Tulkkaus tapahtui koettamalla, tulkkaamalla kahteen ”reikään”, sopiiko GO vai ei NOGO ja korjaamalla ja korjaamalla… Opimme toleranssisuunnittelun, tarkastuksen ja korjauksen tärkeyden!
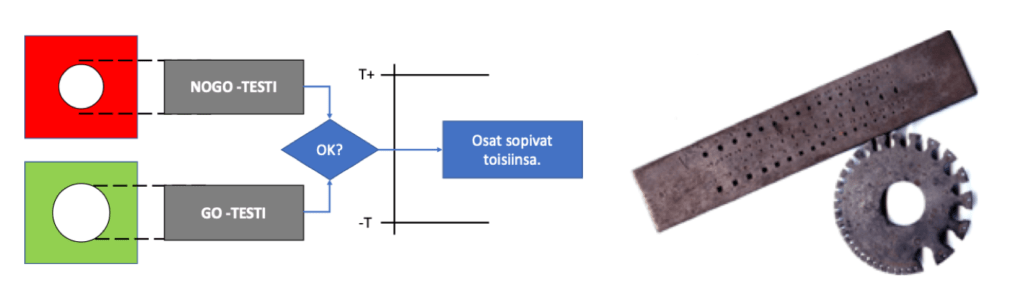
1900-luvun alkupuolella tuli sadan vuoden ikäinen tarkastustoiminta ja korjaus ”rajansa päähän”, kun Western Electricillä (Bell) yritettiin tehdä yhdenmukaisia tuotteita (osia) uudella tavalla, tarkastamalla, parantamalla ja ennaltaehkäisemällä jokainen poikkeama toleranssista. Korjaus yritettiin muuttaa parantamiseksi ja ennaltaehkäisyksi. Ajatus oli jalo, mutta johtikin yhdenmukaisuuden (poikkeamien, vaihtelun, hukan, virheiden ja vikojen) kasvamiseen, mikä oli järjen vastaista. Aivan oikein luettu, virhe- ja hukkamäärät kasvoivat! Miksi parantaminen johti virheiden, hukan kasvuun?
Tri Walter A. Shewhart sai tehtäväkseen selvittää tämän murroksen, paradigman, ristiriidan. 16.5.1924 Walter esitteli ratkaisun ja tästä sai alkunsa uusi yhdenmukaisuuden teoria (laatuteoria), jossa poikkeamat, kansanomaisesti virheet, hukka ovatkin seurausta kahdesta erilaisesta ilmiöstä aikaisemman yhden sijaan. Hän kehitti diagnostiikkamenetelmän, jolla erottelu – jako kahteen luokkaan – voidaan tehdä, kun on yksi samanlainen poikkeama, (symptom) lääketieteessä oire, mutta kaksi eri poikkeaman syylajia, aiheuttajaa. Molemmat poikkeaman, vaihtelun lajit – erityissyy ja satunnaiset syyt (assignable cause, chance causes) – vaativat aivan erilaisen lähestymistavan. Ongelman ratkaisun (korjauksen) ja suorituskyvyn parantamisen (ennaltaehkäisyn).
Menetelmä tunnetaan nykyisin SPC-lyhenteenä (Statistical Process Control) tai ohjauskorttina, laatutauluna, joilla estetään hyvää tarkoittavan toiminnan paha vaikutus ja sallitaan hyvän vaikutus. Laatuteorian mukaan vaihtelut (poikkeamat, virheet, viat, hukka, oire) ovat syntyneet systeemin ulkopuolisesta erityissyyn aiheuttamasta vaihtelusta ja satunnaissyiden systeemin/prosessin aiheuttamista luonnollisista vaihteluista. Useat palvelu- ja tuotanto-organisaatiot kipuilevat tämän ongelman kanssa edelleen. Ne eivät hyväksy tai eivät ole sisäistäneet, miten systeemi ja prosessi käyttäytyy nyt ja tulevaisuudessa. Toimintaa ohjataan, kuten kaikkeen olisi yksi syy – ja ajattelun ja toimenpiteiden mahdollisena seurauksena vaihtelun, virheiden, hukan kasvu.
Vähitellen laatuyhteisö hyväksyi Shewhartin luoman laatuteorian (1950-) ja siirtyi tarkastuksesta SPC:n (laatutaulu) erityissyiden poistamiseen erilaisin ongelmanratkaisukeinoin (laatupiirit, 7 Tools, 8D, A3 jne). Suomessa 1980- luvulta lähtien (Kemppi Oy:n laatutaulut 1981).
Lääketieteessä on myös sama kaksijako, akuutit sairaudet ja krooniset ”sairaudet” (~normaali tila). Diagnostisena menetelmänä viitearvot (www.terveyskirjasto.fi). Akuutit sairaudet ovat lyhytkestoisia (influenssa, haava, murtuma) ja lääkinnällisin keinoin nopeasti hoidettavia ja krooniset sairaudet pitkäkestoisia (verenpainetauti, sydänsairaudet, nivelrikot) ja vaativat pitkäaikaista hoitoa ja lievitystä. Useat potilaat kipuilevat tämänkin tosiasian kanssa!
Lean ja Six Sigma
Our quality sinks” ja Ford, GM ja Chrysler olivat autojen laadun ja tuottavuuden kanssa vaikeuksissa. Japanilaiset veivät markkinoita! Tri W. Edwards Deming esitti haasteen kuuluissa NBC News puheessa If Japan can … Why can’t we? 1980. Hän myös esitti ratkaisun laatu- ja tuottavuuskriisiin kirjassaan Out of the Crisis 1982, joka käsitteli uutta johtamistapaa ja parantamista, Improve quality. Hän esitti kirjassaan kuuluisan tuottavuuden ketjukuvan, joka alisti tuottavuuden kehittämisen laadunparannukselle, jossa kaiken päämääränä on tarjota enemmän työtä ja taas työtä. Deming täydensi parannuksen teoriaansa kirjassa The New Economics 1993 ja antoi sille nimen Syvällisen Tiedon Systeemi (System of Profound Knowledge, SoPK).

Ongelmana oli, että SPC:n tarjoama erityissyiden ja ongelmien ratkaiseminen ei näyttänyt tuovan riittävää kilpailukykyä! Suorituskyvyn parantamiseen ei yleisesti ollut käytettävää ratkaisua, parannuskeinoa. Kuinka ihmeessä selvitetään satunnaisten tekijöiden joukosta kausaalitekijöiden verkko? Mikä on tulevaisuuteen vaikuttavien kausaalitekijöiden takana? Vain harva syy on kausaalitekijä!
Tri J. M. Juran esitti tosin jo vuonna 1964 satunnaisten syiden aiheuttamien poikkeamien (suorituskyvyn) hallitsemiseksi parannustekniikan, läpimurtotekniikan (Managerial Breakthrough), mutta menetelmä ei levinnyt ennen kuin Motorolassa kehitettiin tämän ja Demingin ajatusten pohjalta erityinen salainen looginen suodatin, kausaalisuodatin ja tästä rekisteröity, suojattu Six Sigma -menetelmä 1987, joka avattiin yleiseen käyttöön 1998 (Quality Progress, 10/1998). Ongelmana oli ja on edelleen, kuinka satunnaisesta prosessista löydetään, ”suodatetaan” syy-seuraus eli kausaali rakenne esille. Tätä kutsutaan laatukielellä juuri-syyksi, joka on eri asia kuin syy. Tämä ongelma vaivaa erityisesti tekoälyn (AI) kehittämistä, kuten tri Judea Pearl kirjoissaan Miksi – Syyn ja seurauksen uusi tiede 2018 ja Causality 2009 toteaa. Tri Pearl esittää kolme kausaalisuuden porrasta: assosiaatio, interventio ja kontrafaktuaalit. Interventio on asioiden muuttumiseen johtava porras, jolle on päästävä (löydettävä), jotta syy on kausaalisyy, johon voidaan kohdistaa parannustoimenpide. Ainakaan vielä tekoäly ei kykene syy-seuraussuhteen, kausaalisuuden kuvaamiseen. Vain kausaalisuus johtaa ennaltaehkäisyyn, parannukseen. Juuri-syy eli kausaalisuus voidaan löytää ja todentaa VAIN kokeella, Design of Experiment. Parannus ei onnistu ilman mallia ja koetta (DE, DoE, Design of Experiment). Siksi myös Leanissa korostetaan jatkuvasti Demingin PDSA-koeympyrää. (Lääketieteessä kausaalia – syy-seuraus – parannusta vastaa lähinnä uusi lääke tai rokote, jotka nekin vaativat kokeellisen osion.)

Six Sigmassa minimitavoitteeksi asetettiin 6 sigma taso, josta seuraa, että suorituskykyindeksit on saatava vähintään Cp>2 ja Cpk>1,5. Tämä tarkoitti normaalin 10-30% virhetason pudottamista 0,00034%:n tasoon ja samalla mahdollistaa monimutkaisempien kokonaisuuksien valmistamisen vikavapaasti, jolloin saavutetaan suuri noin 20% tuottavuusparannus. Tätä oli jo aikaisemmin haikailtu Philip Crosbyn 0-virhe kirjassa ”Laatu on ilmaista” (Quality is free 1979). Todettakoon, että suomalaisen yrityksen normaali suorituskyvyn indeksiarvo Cpk on edelleen 0,3-0,7, joka tarkoittaa noin 5 -30% virhetasoa. Tämä näkyy arjessa samojen asioiden toistuvana uudelleentekemisenä ja korjauksena sekä isona määränä erityyppisiä testauksia ja taas korjauksina ja säätöinä.
Toyota oli kehittänyt ja hyödyntänyt suorituskyvyn kautta tapahtuvaa tekniikkaa autojen suunnitteluun ja tuotantoon 1950-luvulta lähtien Demingin ja Juranin opastuksella. 1977 tuli julki Toyotan (Japanin) autoteollisuuden ällistyttävät tuotannolliset saavutukset, jotka kääntyivät lännessä 90-luvulla TPS:ksi (Toyota Production System) ja myöhemmin 2000-luvun vaihteessa Leaniksi. Erityisesti huomiota kiinnitettiin tuotannon (liukuhihnan) virtaustehokkuuteen ja jaksoaikoihin, joiden heikkouden lähteeksi nimettiin liike hukka (waste of motion), jota kaikessa toiminnassa on vältettävä. Hukka jaettiin edelleen lukuisiin eri luokkiin. Mutta mikä on hukan kausaalisyy?
Professori Kakuro Amasaka (Toyotan laatujohtaja 1968-1997) yhdistää TQM:n ja TPS:n (Six Sigman ja Leanin) yhdeksi ja samaksi malliksi, jossa TQM:llä ja SQC:llä, Scientific Quality Control, on pienennetty vaihtelua (fluctuation) ja parannettu suorituskykyä, joka on mahdollistanut tuotannon keskiarvojen muuttamisen ja virtaustehokkuuden nostamisen. (Japanilaisten Cpk-indeksi >4,5 1992.) Hukan kausaali (syy) on siis vaihtelu (fluctuation), jonka mittarina on sigma, keskiarvon keskipoikkeama. Vaihtelun pienentäminen tapahtuu hyvin saman tapaisella menetelmällä, kausaalisuodattimella, kuin Six Sigmassa (Logic filter). Amasaka kuvaa menetelmää lyhenteillä N7, MA, DE (TQC:n 7 uutta laatutyökalua, monimuuttuja-analyysi (MA), Design of Experiments (DE))
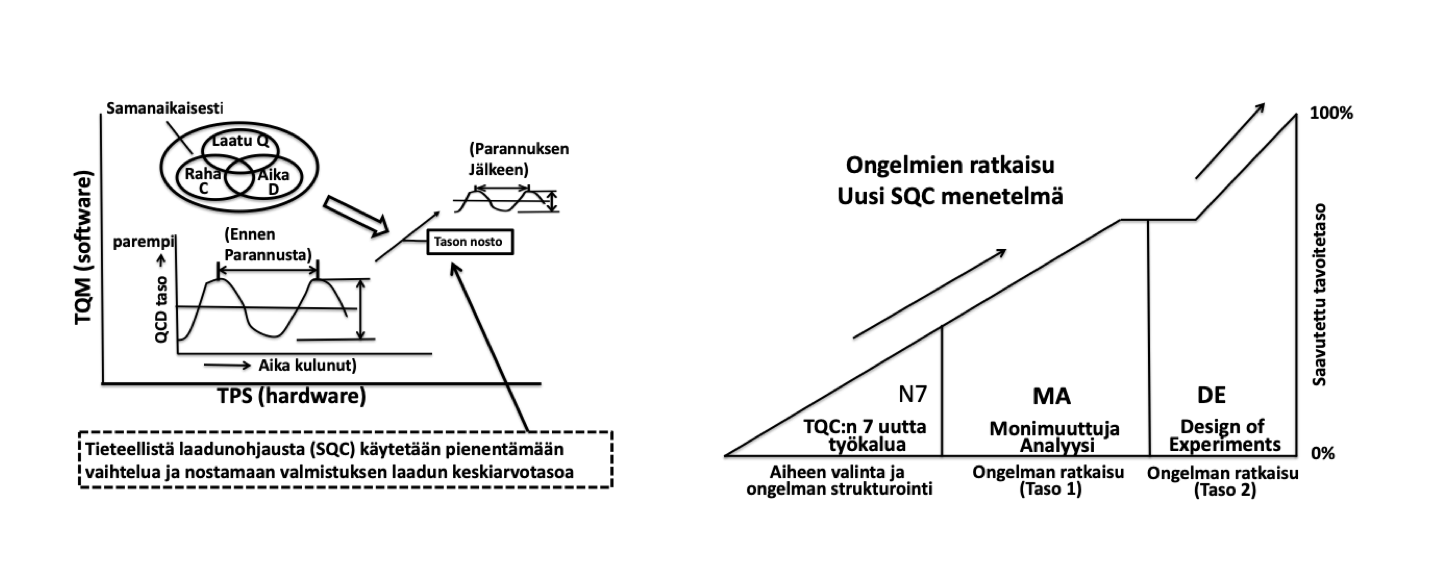
Pienen vaihtelun (korkean suorituskyvyn ja stabiilisuus) vallitessa erilaiset liikehukat (waste) tulevat selkeästi esille ja niitä on mahdollista hallita pelkästään keskiarvoja muuttamalla ja siirtämällä, koska keskiarvon keskivirhe pienenee ja tarvittava näytekoko lähenee yhtä. Ongelman ratkaisu ja koneiden ja työmenetelmien kehittäminen tulee helpoksi ja se voidaan levittää koko organisaatiolle ja tuottavuus kasvaa kaikkien toimesta (TQM). Tämä sama ilmiö tapahtui muskettien valmistamisessa. Vaihdetavien osien (toleranssien) myötä monimutkainen 50 osan musketti voitiin ”jakaa” 50:n yksinkertaisemman itsenäisen osan valmistamiseen, joka on 50 kertaa helpompaa ja johon voi osallistu yhden henkilön sijaan 50 henkilöä ja heidän osaamisensa!
Leanin ja Six Sigman takana on sama ilmiö, vaihtelu, mutta nyt hallintakeinona ei ole fyysinen toleranssi vaan abstrakti käsite vaihtelu. Niinpä Lean integroitiin Six Sigmaan 2002 tri Michael Georgen toimesta kirjassa Lean Six Sigma.
Lean ja Six Sigma ei ole koko totuus laadusta!
Lean ja Six Sigma ei ole koko totuus laadusta ja laatuteknologiasta. Laatuteknologia on paljon muutakin. Yritysten olisi kehitettävä ja ylläpidettävä kaikkia laatuteknologian osa-alueita tasapuolisesti yrityksen tarpeita painottaen aina tuotteiden ja palveluiden suunnittelusta lähtien ja päätyen asiakkaaseen.
Asiakkaiden tarpeet on otettava huomioon, pyritään sitten asiakastyytyväisyyteen tai hyvään asiakaskokemukseen. On olemassa lukuisia suunnittelumenetelmiä, jotka yrityksessä olisi tunnettava ja käytettävä vaihtelun (riskin) hallitsemiseksi, jotta tyytyväisyys ja kokemus saavutetaan minimikustannuksin ja voidaan kasvaa ja tarjota työtä ja taas työtä (Deming).
Kuinka moni palvelu ja tuotanto organisaatio tuntee ja osaa asiakaslähtöisen tuotekehityksen, QFD:n menetelmät ja toleranssit ja toleranssien asettamisen, joita kutsutaan myös spekseiksi, vaatimuksiksi. Ovatko ne mielekkäät ja oikeat ja syntyykö ”osista” kokonaisuus vai kaaos?
Vaikka käytetään tehokkaita menetelmiä suunnitteluun, on tuotannon ja palvelun prosesseja ohjattava ja hallittava oikeilla menetelmillä. Miten tapahtuu palvelun ja tuotannonohjaus? Onko estetty vaihtelun kasvu? Väärä menetelmä vain kasvattaa vaihtelua kuten Western Electricillä 1920-luvulla ja monessa, monessa suomalaisessa yrityksessä juuri tällä hetkellä!
Laadunohjaustekniikoita on lukuisia itseohjauksesta SPC:n kautta auditointeihin ja erilaisiin standardeihin. Tämäkään ei riitä, myös lopputarkastuksella on edelleen pystyttävä erottelemaan vialliset tuotteet ja palvelut toisistaan. Maailma ei ole täysin ennustettavissa! Toimiiko lopputarkastus? Karkea arvioni on, että yli 50%:ssa yrityksiä tuotteiden lopputarkastus ei toimi. Tarkastuksella ei silloin ole suoraa syyvaikutusta (kausaalia) toimitettaviin tuotteisiin ja palveluihin. Meillä ei silloin ole myöskään tapaa parantaa tuotantoprosessia.
Asiakasreklamaatioihin ja valituksiin on vastattava ja reagoitava oikein, jotta valitukset eivät tämän toiminnan ansiosta ainakaan kasva (valitus = poikkeama, johon on kaksi eri syymekanismia). Paraneeko laatu yksittäisiä reklamaatioita tutkimalla, epäilen! Millä menetelmällä kausaalitutkimus yksittäisen reklamaation osalta olisi suoritettava? Vaatii laajoja analyysejä, kokeita ja aikaa, kuten lentokoneiden onnettomuuksien tutkinta.
Parhaimmista parhaimmat
Laatuteknologian soveltaminen ei vain pelasta yrityksiä ongelmilta, vaan nostaa yritykset parhaimmista parhaimmiksi, joita seuraamme ja otamme oppia. Toyota oli Japanin laatupalkinnon (Deming Prize) voittaja ja siitä on seurannut maailman menestys ja Lean. Motorola voitti ensimmäisen USA:n presidentin laatupalkinnon 1988 Six Sigmalla ja siitä seurasi Six Sigma.
Olemme saaneet olla mukana lukuisten suomalaisten yritysten menestyspolulla yli 30 vuoden ajan. Henkilökohtaisesti olen saanut osallistua usean kymmenen vuoden ajan lukuisten yritysten laadun seurantaan ja erityisesti neljän yrityksen laatupolkuun kohti Suomen laatupalkintoa (Kemppi Oy 1986, Stala Oy 1991, 1992, Salpausselän kirjapaino Oy 2000). Nämä ja monet muut yritykset ovat viitoittaneet uutta polkua laadun sarallamme. (Lue artikkeli: 10 + 20 vuotta laatukoulutusta – Laatutieto Oy:stä Quality Knowhow Karjalainen Oy:n).
Olemme ”testanneet” erilaisia laatumenetelmiä eri yrityksissä ja niiden toimivuutta suomalaisessa ympäristössä. Testituloksista olemme julkaisseet erilaisia tutkimuksia ja yhteenvetoja. Kirjoja, artikkeleita, blogeja on yli 200. (Kaikki artikkelit löytyvät täältä: QKK Artikkelit). Kiitoksia kaikille näille yrityksille, jotka ovat jakaneet tietoa ja mahdollistaneet julkaisut.
Lean ja Six Sigma -koulutus sekä sen yhteyteen kuuluva sertifiointiprosessi (Black Belt ja Green Belt -loppuraportti) tuo edelleen päivittäin ja kuukausittain aivan käsittämättömän hienoja liiketoiminnan parannuksia (case). Toivottavasti voimme ainakin osan parannusten opeista jakaa kurssiemme välityksellä, vaikka suurin osa yritystiedoista on luottamuksellista tietoa.
Menestysten takana on aina ripaus onnea ja paljon tietoa ja taitoa. Tieto ja taito on kaikkien hankittavissa ja toivon mukaan rakentuu kuitenkin pääosin VAIN tieteellisen (lue: todistetun vaikutuksen omaava) laatuteknologian ja tekniikan soveltamisen varaan. Tämä on tehokkain ja riskivapain konsepti.Suosittelemme kaikkia tutustumaan kohta ilmestyvään modernin laatuteknologian menetelmiin ja soveltamiseen johdattavaan kirjaan Lean Six Sigma 2.0 ja Laatuteknologia.
Katso YouTube -videolta kirjaan liittyvä haastattelu:
Lähteet:
- Karjalainen E & T: Lean Six Sigma 2.0 ja Laatuteknologia, 2020, julkaistu 12.10.2020
- Heidi Kanninen, Harri Puolitaival: Tekoäly – Bisneksen uudet tuulet, 2019
- Judea Pearl, Dana Mackenzie: Miksi – Syyn ja seurauksen uusi tiede, 2018
- Judea Pearl: Causality – Models, reasoning and inference, second edition, 2009
- Judea Pearl, M. Glymour, N. Jewell: Causal inference in Statistics, 2016
- Kakuro Amasaka: Science SQC, New Quality Control Principle – The Quality Strategy of Toyota (2004)
Tutustu kurssitarjontaamme!
Tilaa uutiskirje
Liity postituslistalle ja saat uusimmat artikkelit suoraan sähköpostiisi.
Tämä lomake on suojattu Google reCAPTCHA:lla. Lue tietosuojaseloste ja käyttöehdot.
Liittymällä postituslistalle hyväksyt Quality Knowhow Karjalainen Oy:n tietosuojaselosteen ja Quality Knowhow Karjalainen Oy voi lähettää sinulle ajankohtaisia artikkeleita, videoita sekä tietoa ja tarjouksia kursseista, kirjoista sekä ohjelmistoista.
Tämä lomake on suojattu Google reCAPTCHA:lla. Lue tietosuojaseloste ja käyttöehdot.