Lukuisissa yrityksissä vannotaan asiakaspalautteiden nimiin. Halutaan kuunnella asiakasta herkällä korvalla. Yrityksissä uskotaan palautteen keräämisen ja tutkimisen parantavan laatua ja tuottavuutta. Valitettavasti näin helppoa se ei ole! Vain 1-3% liikkeenjohdon käynnistämistä parannuksista, jotka usein perustuvat asiakasvalituksiin ja reklamaatiokustannuksiin, johtavat merkittäviin tuloksiin.
Asiakaspalautteita, tuotepalautuksia, takuukorjauksia, reklamaatioita, millä nimellä niitä nyt kutsutaankin, tulee kaikille yrityksille kymmenistä satoihin tuhansiin. Itse olin eräässä yrityksessä laatupäällikkönä 1980-luvulla. Reklamaatioita, takuu-korjauksia tuli yli 40 000 kpl/vuosi joka vuosi. Onnistuin vähentämään reklamaatioita 95% mutta en reklamaatioita tutkimalla vaan päinvastoin olemalla tutkimatta! Albert Einstein on sanonut: ”Emme voi ratkaista ongelmia käyttämällä samaa ajattelua, jota käytimme niiden luomisessa.” Reklamaatio-ongelmaa ei voi ratkaista tutkimalla reklamaatioita!
Yritykset kuluttavat huimia määriä työvoimaa ja resursseja palautteiden tutkimiseen ja asiakaskorvauksiin. Tämä jatkuu vuodesta toiseen eikä parannusta näy. Palaute- ja reklamaatiokäyrät, laatukäyrät, matelevat samalla tasolla. Ei parannusta, laatu- ja hukkakustannukset ovat 20-45% luokkaa jalostusarvosta joskin raportoidut 2-4%.
Mikä on ongelma? Miksi reklamaatioselvitykset ja tutkimukset eivät auta ja laatutaso parane?
En usko, että ongelma on asiakaspalautteiden tai selvitysten määrässä vaan niiden laadussa. Asiakaspalautteet ovat oireita, jotka johdattavat usein tutkimaan väärää asiaa väärin. Ongelmana on siis väärän asian selvittäminen väärällä menetelmällä ja tästä seuraava väärän asian muuttaminen! Seurauksena on reklamaatiomäärien kasvu, joka taas on välttämätön seuraus (vääristä) toimenpiteistä.
Ongelma ei ole tuntematon laatutekniikassa. Six Sigma syntyi tutkimuksesta, jossa Motorolan tri Bill Smith/1,2/ selvitti 1984 yhteyttä tuotteen kenttäeliniän (field Life) (so. reklamaation) ja tuotteen tuotannossa tapahtuvien korjausten lukumäärän välillä. Ongelmana oli jo useita vuosia jatkunut Motorolan laatutason heikkeneminen korjaustoimenpiteistä huolimatta tai jopa niistä johtuen. Bill julkaisi sisäisen tutkimuksen piilevistä vioista – ”internal paper relating product failures to latent defects” 1985. Hän päätyi tässä tutkimuksessa Six Sigman teoriaan:
”Jos tuote on löydetty viallisena ja korjattu tuotanto-prosessissa, muut viat jäävät löytymättä ja löytyvät myöhemmin käytön aikaisessa vaiheessa. Jos tuote valmistetaan virhevapaana, se harvoin vioittuu käytön aikaisessa vaiheessa”.
Kuinka toteuttaa täysin virheetön tuotanto- ja palveluprosessi?
Reklamaatioiden tiheys ja rakenne voidaan esittää luotettavuuskäyränä eli ammekäyränä/3/, josta karkeasti ilmenee, mistä reklamaatiot, asiakasvalitukset muodostuvat tuotteen ja palvelun käytön aikana (field life).

Ammekäyrä on jaettu kolmeen jaksoon, sisäänajo (lapsikuolleisuus), käyttöaika, kuluminen. (I infant mortality, III useful life, III wearout). Käyrä on edelleen jaettu vaikutuskomponentteihin, laatuvirheet, suunnitteluperusteiset virheet ja kulumisvirheet (quality failures, design-related failures, wearout failures).
Reklamaatiot ja valitukset ns. early life failure eli latentit viat, tulevat ensi sijassa laatuvirheistä. Latenttien vikojen syiden, laatuvirheiden, paljastamiseksi, Motorol tri Mikel Harry/4/, Six Sigman keskeinen kehittäjä, loi vuonna 1985 loogiset suodattimet (The Logic filters), jolla reklamaation syyt voidaan paljastaa. Tämä oli esiaste Six Sigmaan.
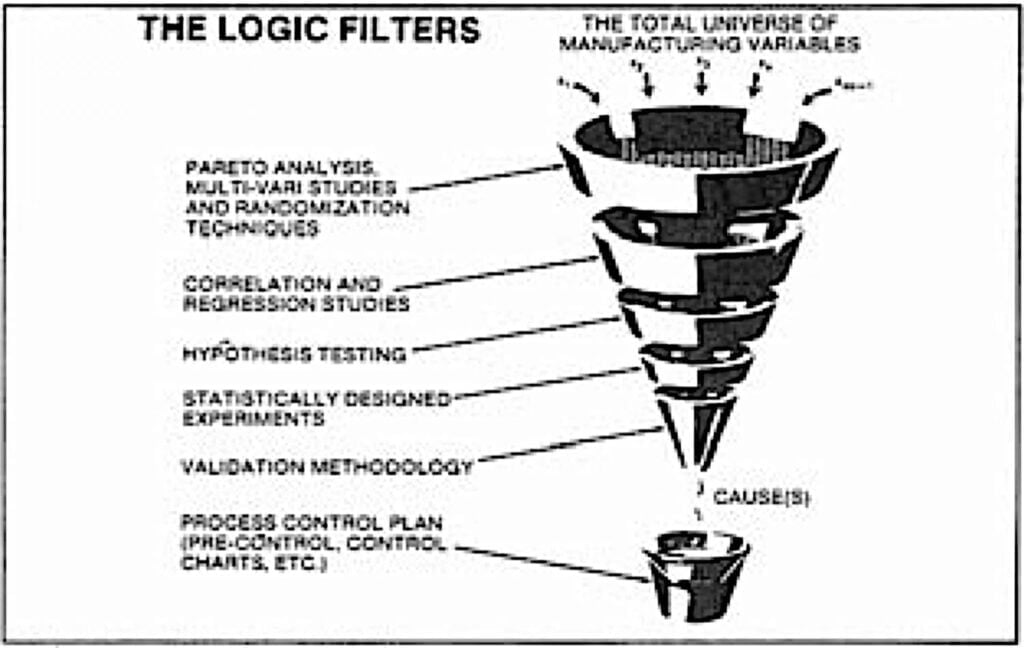
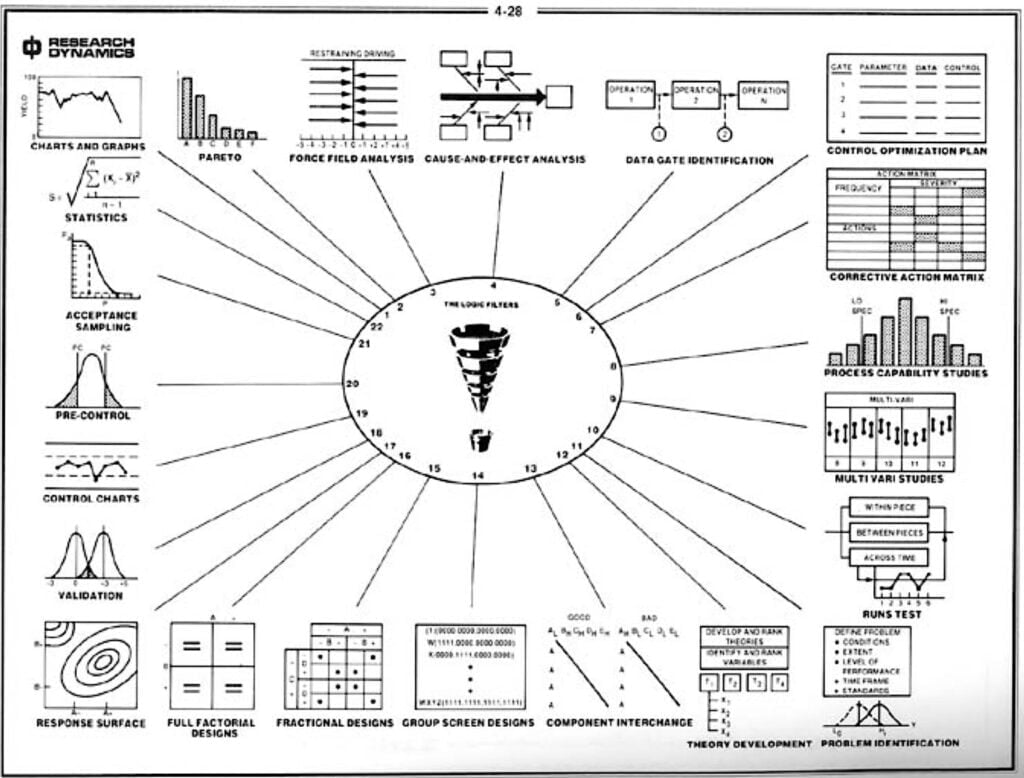
Yksittäisestä reklamaatio- tai palauteanalyysistä reklamaation selvittäjä tai analysoija ei yleensä pysty päättelemään reklamaation syytä etenkään, jos hän ei hallitse Lean Six Sigmaa ja sen menetelmiä (looginen suodatin). Seuraavassa lyhyt ”oppimäärä” loogisen Six Sigma DMAIC-suodattimen käytöstä reklamaatioihin.
Miten laatuvirheet hävitetään so. reklamaatiot ja valitukset
Suuri osa ongelmista, virheistä (94-98%) on systeemin suorituskyvyn heikkoutta siihen nähden, mitä yritetään saavuttaa. Tälle ei ole olemassa helposti selvitettävissä olevaa faktasyytä. Tämä on tieteeseen perustuvan laadunohjauksen (SQC) näkemys laatuongelmista/5/. Eksaktia maailmaa, jossa jokaiselle asialle on tarkka selitys, ei ole olemassa, mutta asiat, yksittäisten asioiden aiheuttama sumeus, voidaan tarkemmin kuvata tilastollisilla jakaumilla aivan kuin elektroni ytimen ympärillä. Tämä tarkempi kuvaus mahdollistaa kausaalisyiden, ideoiden paljastamisen.
Tilastollisen jakauman ”pilkkominen” vaikuttaviksi tekijöiksi, parametreiksi ei onnistu kuin kokeen (DOE) avulla luotettavasti. Siksi kaikissa parannusalgoritmeissa on Demingin PDSA-ympyrä, koeympyrä. Näennäiset korrelaatiot ja yhteydet, poikkeamat eivät johda reklamaation syyn selviämiseen ja parannukseen.
Kuinka teollisuus ja palvelu ovat ”selättäneet” reklamaatiot’, jos syytä ei voi helposti selvittää?
I Toleranssit ja tarkastus
Reklamaatioita ja asiakaspalautuksia voidaan vähentää, kun eksaktit asiat ilmaistaan tarkemmin (tilastollisilla) toleransseilla (Total Range) ja lisätään tähän perustuva erotteleva tarkastus ja korjaus tuotantoprosessin loppuun. Erottelevalla tarkastuksella poistetaan ei-suorituskyvykkäät komponentit, tuotteet ja palvelut eli ”leikataan” jakaumaa kuten sonnista filettä ja loppu makkaraksi! (tai palvelu uusiksi)

Ensimmäinen tehtävä reklamaatio- ja palauteselvityksissä on tutkia, toimiiko erotteleva tarkastus. Miksi se vuotaa? Onko rajat laitettu oikein?
Olen huomannut, että yli 50% yrityksistä, joilla on suuret reklamaatiomäärät, tarkastus ei toimi niin kuin sen pitäisi toimia. Kukaan ei ole selvittänyt tarkastuksen kyvykkyyttä erotella hyviä huonoista. Tarkastusrajoja asetettaessa ei ole huomioitu tarkastusprosessin virhettä eli vedetty rajoja riittävästi sisäänpäin (2σe) toleranssi-rajoista. Unohdetaan myös virheen kertautuminen. Jos tarkastat 10 kohtaa tuotteesta 95% oikeellisuudella lopputulos on 60%:sti oikein ja 40% väärin (P=0,9510 = 0,598). Mitä useampia kohteita on tarkastettavana sitä vaikeampi on välttyä reklamaatioilta!
Tarkastuksen kyvykkyyden voi testata karkeasti käyttämällä prosessin ja/tai tarkastuksen hylkäys- ja reklamaatiodataa samalta ajanjaksolta. Tämä data löytyy lähes aina. Yleensä data on viikko-, kuukausidataa, jossa datat on kohdistettu toisiinsa. Kohdistus ei tarvitse olla tarkka. Riittää, jos voidaan liittää saman aikavälin datat esim. valmistusnumeron mukaan. Syntyy datapareja (pisteitä), jotka voi asettaa XY -akseleille. Jos muodostuu suora, kuten kuvassa vasemmalla erottelu toimii ja kulmakerroin kertoo, kuinka paljon erottelu vuotaa.
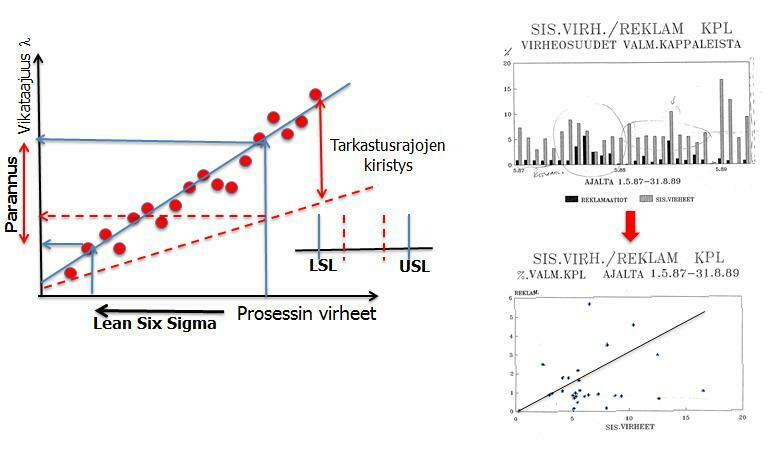
Jos ei muodostu selkeää korrelaatiosuoraa, tarkastus ei erottele ja toimi, kuten erään yrityksen tarkastus vuosina 1987-89. Viat ja virheet menevät hallitsemattomasti asiakkaille, josta seuraa asiakasvalitukset ja reklamaatiot. Kuva 5.
Six Sigman MSA-analyysillä ja mielellään Minitab Assistantilla voidaan myös selvittää, voiko mittauksella erotella osat ja toisaalta soveltuuko mittaus prosessin ohjaukseen / suoritusarvon määrittämiseen. Tuloksen saa havainnollisena palkkikuvana. Vihreä on hyväksyttävä ja keltainen ”ehkä” hyväksyttävä ja punainen hylättävä.
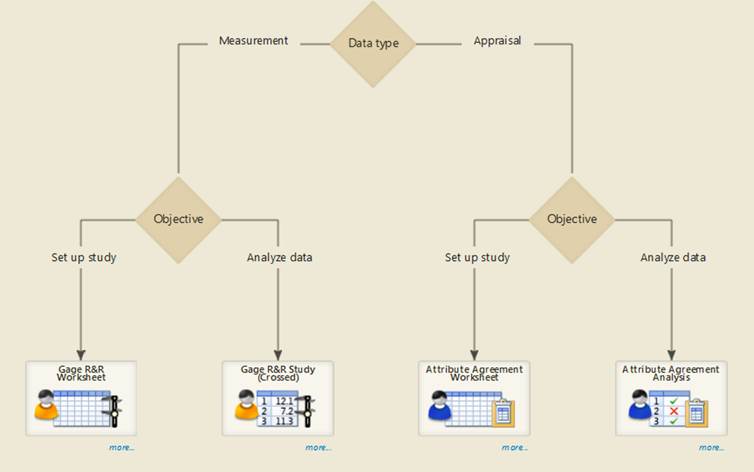
Jos erotteleva tarkastus toimii, tarkastusrajoja LSL, USL kiristämällä (Kuva 5) reklamaatioita ja palautuksia voi vähentää, mutta samalla turhaan hylättyjen tuotteiden määrä ja kustannukset kasvat. Prosessin virheitä on vähennettävä suorituskykyä parantamalla.
II Prosessin stabiilisuus ja erityissyy
Jos erotteleva tarkastus toimii, seuraava vaihe reklamaatiotutkimuksessa on selvittää prosessin stabiilisuus ja mahdollisuus erityissyyvirheiden poistamiseen prosessista. Laatutauluilla ja SPC:llä/6/ prosessia voidaan ohjata oikein ja poistaa erityissyyt (2-6%) muutamassa viikossa. Apuna voi käyttää 8D:tä. Kuva 4. Tämä avaa mahdollisuuden prosessin parantamiseen.
III Prosessin suorituskyvyn parantaminen, latentit virheet (Lean Six Sigma)
Kolmas vaihe on suorituskyvyn parantaminen, joka kattaa 94-98% reklamaatioista. Tähän voi käyttää Lean Six Sigma -menetelmää/7/ tai jotain muuta sovelletun tilastotekniikan (applied statistics) menetelmää (kuva 4), joilla luodaan looginen suodatin. Menetelmällä EI haeta varsinaista syytä vaan ideaa tai ratkaisua siihen, kuinka systeemin/prosessin suorituskykyä voidaan parantaa niin, että suorituskykyindeksi Cp>2 eli virheitä vähemmin kuin 3,4 kpl/miljoona mahdollisuutta. Toyota käyttää tästä nimeä tieteellinen laadunohjaus SQC/TQM. Menetelminä ovat N7 – MA – DE./8/
IV Tuotesuunnittelu ja luotettavuustekniikka
Neljännessä vaiheessa siirrytään reklamaatiotutkimuksissa luotettavuustekniikkaan tarkastelemaan itse suunnittelua, miksi tuotteeseen/palveluun kohdistuva rasitusjakauma, kuorma L, leikkaa suunnittelun määrittämän kestävyysjakauman eli lujuuden S. Lujuusjakauman leveys mitattuna sigmoissa kertoo tuotteen suorituskyvyn 6σ. Tämä esitetään yleensä toleransseihin verrattuna eli Cp=(T+-T+)/6σ. Six Sigmassa asetetaan suunnitteluvaatimus Cp > 2. Tämä on osa DFSS-tekniikkaa (Design for Six Sigma). Menetelmä tunnetaan myös käsitteellä Robust Engineering tai Taguchi-menetelmänä.

Hajontaan 6σ:aan vaikuttaa suunnittelu, materiaalit ja komponentit ja valmistusprosessi, joita voidaan suunnitella ja analysoida luotettavuustekniikan menetelmin./9/
Yhteenveto
Reklamaatiot ja asiakaspalautteet ja niihin liittyvät toimet maksavat yrityksille todella paljon ja tahraavat yritysten mainetta. Reklamaatioita ja asiakaspalautteita selvitetään usein väärin ja tehdään muutoksia vääriin kohtiin.
Olen kaikille asiakasyrityksille suositellut nykymuotoisten yksittäisten asiakas- ja reklamaatiopalautteiden tutkimisen lopettamista ja panosten siirtämistä suorituskyvyn parantamiseen. Kun yrityksissä on näin toimittu, yrityksien reklamaatiot ovat lähteneet jyrkkään laskuun, kun samalla on noudatettu edellä kuvaamaani menettelyä, joka on täysin ISO 9001 mukainen. Asiakaspalautteita ja reklamaatiotietoja tulee seurata SPC-käyrillä ja jos tulee erityissyy, on tällöin ja vain tällöin selvitettävä reklamaation syy välittömästi.
Reklamaatioita ja palautteita on aina seurattava ja tällä indikoitava, toimiiko erotteleva tarkastus, prosessin ohjaus ja jatkuva suorituskyvyn parannusprojektit ja suunnittelu. Jos reklamaatiot ja palautteet eivät kehity oikeaan suuntaan oikealla yrityksen toivomalla nopeudella, on ongelmaan puututtava. Itsestään selvää on, että jokainen asiakas on oikeutettu saamaan korvauksen ja riittävän huomion huonosta tuotteesta ja palvelusta. Reklamaatio ja palauteselvityksen tavoitteena on ennaltaehkäistä tulevat reklamaatiot.
Lähteet:
- https://www.isixsigma.com/new-to-six-sigma/history/remembering-bill-smith-father-six-sigma/
- Mikel J. Harry, Richard Schroeder: Six Sigma – the Breaktrough Management Strategy Rovoluzionizing the World’sTop Corporations (2000) sivulla 10
- Mikel J. Harry, J. Ronald Lawson: Six Sigma Productivity Analysis and Process Characterization (1992)
- https://www.mikeljharry.com/milestones.php
- Walter A. Shewhart: Economics Control of Quality of Manufactured Products. (1931)
- http://www.qk-karjalainen.fi/fi/artikkelit/unohdettu-laadunohjaus/
- Artikkeli: ”Kultasormi” Black Belt ja hänen Lean Six Sigma -pelinsä
- Artikkeli: Toyota ja Lean – Mikä on Leanin lähestymistapa laatuun
- Patric D. T. O’Connor: Practical Reliability Engineering, Fourth Edition (2002)
2 kommenttia aiheesta “Auttavatko palaute- ja reklamaatioselvitykset parantamaan laatua?”
Kommentoi artikkelia
Tämä lomake on suojattu Google reCAPTCHA:lla. Lue tietosuojaseloste ja käyttöehdot.
Tutustu kurssitarjontaamme!
Tilaa uutiskirje
Liity postituslistalle ja saat uusimmat artikkelit suoraan sähköpostiisi.
Tämä lomake on suojattu Google reCAPTCHA:lla. Lue tietosuojaseloste ja käyttöehdot.
Liittymällä postituslistalle hyväksyt Quality Knowhow Karjalainen Oy:n tietosuojaselosteen ja Quality Knowhow Karjalainen Oy voi lähettää sinulle ajankohtaisia artikkeleita, videoita sekä tietoa ja tarjouksia kursseista, kirjoista sekä ohjelmistoista.
Terve, Eero!
Hyvä artikkeli taas, taattua laatua!
Vallalla tuntuu olevan olettama, että jokaisen reklamaation takaa löytyy jokin syy (puhekielessä ’juurisyy’), jonka poistamisessa vakaasti uskotaan onnistuttavan, mikä sitten tosissaan nähdään suorituskyvyn parantamisena. Perusongelma, että suorituskykyä ei tarkastella hajontojen kautta, ainoastaan diskreettien tapahtumien ilmentymänä.
Kiitos kommentista
Näinhän se on. Jokaiseen reklamaatioon on kyllä joku korjaus tai ainakin hyvitys mahdollista tehdä. Useat ajattelevat, että tämä riittää myös reklamaation parannukseksi, ennaltaehkäisyksi. Miten tämä ajatus on niin vaikea? Miten joku voi uskoa tälläistä?
Ennaltaehkäisy on huomattavasti vaativampaa ja vaatii todellisen juurisyyanalyysin ja kausaalitekijän löytämisen. Olen näistä käsitteistä kirjoittanut useita artikkeleita.
Otanpa yhden esimerkin. Sairastut nuhakuumeeseen. Tämän korjaamiseen riittää kuumelääke. Ehkäiseekö tämä tulevat nuhakuumeet? Todennäköisesti ei. Suoritat juurisyyanalyysin ja määrität viruksen. Vaativaa! Onko tämä riittävää? Todennäköisesti ei. Millä estät virukset nenästäsi? Mikä olisi kausaalitekijä? Pesemällä nenääsi?! (Vertaus avaimen etsimisestä lampunalta.) No ei, vaan pesemällä saippualla käsiä riittävän usein ja aina kun tulet yleisistä tiloista tai tapaat ihmisiä. Eikö ole yllättävää ja yllättävä ratkaisu kuten yleensä aina reklamaatioratkaisut. Toimii. Tämän todisti data koronanan aikana. Kausi infulenssa jäi tulematta.