Osataanko hyödyntää tietokonetta informaatioaikakaudella datan käsittelyyn? Tietokoneita käytetään kirjoituskoneen ja perinteisen postin korvaavaan toimintaan? Tämäkin tuo ”tehokkuutta”, mutta tuoko riittävästi, vai tukkiiko helppous meidät ajankäytön.
Mitä meidän tulisi tehdä ja penkoa informaatiosta? Mikä aiheuttaa muutosta ja parantaa laatua tai tehokkuutta ja mikä on ekonomisesti tehokasta parantamista?

Numeronaivius – kertaus
Kaiken uuden tiedon – parannuksen – luomisessa on kysymys vertaamisesta. Onko mennyt tapahtuma tai aiheutuuko muutos tulevaisuudessa. Edellisessä artikkelissa käsiteltiin datan keräystä ja tulkintaa. Data syntyy joko toiminnan tuloksena (Observational Studies) tai kokeellisena (Experimental Studies) datana. Datasta voidaan havaita muutoksia – signaaleja: outlier, siirtymä ja trendi (Huom! tämä on vertailua normaalitilanteeseen). Seuraava looginen kysymys on, mistä nämä signaalit johtuva?
Vaihtelun perussyy – Juurisyy – Root Cause
Mikä on vaihtelun perussyy – juurisyy. Tämä on perustavaa laatua oleva kysymys, joka kiinnostaa kaikkia. Lääketieteessä keskustellaan, mistä sairaudet johtuvat. Seuraavien kappaleiden tarkoituksena on kuvata, mitä tulisi löytää. Mitä on ekonominisesti järkevä selvittää ja tutkia?
Kun on tehty ero rutiinivaihtelun ja poikkeuksellisen vaihtelun välillä, olisi hyvä olla tälle vertailulle konseptuaalinen malli, joka kertoo näiden kahden erilaisen vaihtelun alkuperän. Seuraavana käsitellään tätä mallia, sen kokemuksen mukaan, jota Six Sigma BB-projektit ovat tuoneet.
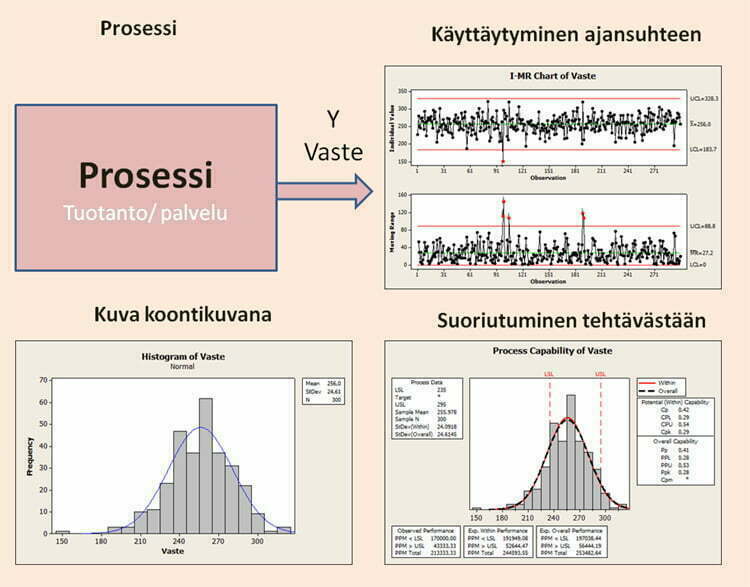
Ajattele, että käytössäsi on jokin yksi mitattu tuotteen ominaisuus, palvelu, jota tarjoat asiakkaille. Yleisesti tätä kutsutaan prosessin ulostuloksi Y:ksi, josta tiedät jotain: paikka – missä, leveys – kuinka hyvä ja vaatimukset – päämäärä (keskiarvo, sigma ja speksit – kuva 2)
Listaa mielessäsi kaikki mahdolliset syy-seuraussuhteet, jotka vaikuttavat ulostuloon. Saat kymmeniä, satoja jopa tuhansia vaikuttajia! Mitä innovatiivisempi olet tai tiimisi on, sitä laajempi on muuttujien joukko. Ulostulossa havaittavan vaihteluun vaikuttavia tekijöitä on kuvattu kuvassa 4.
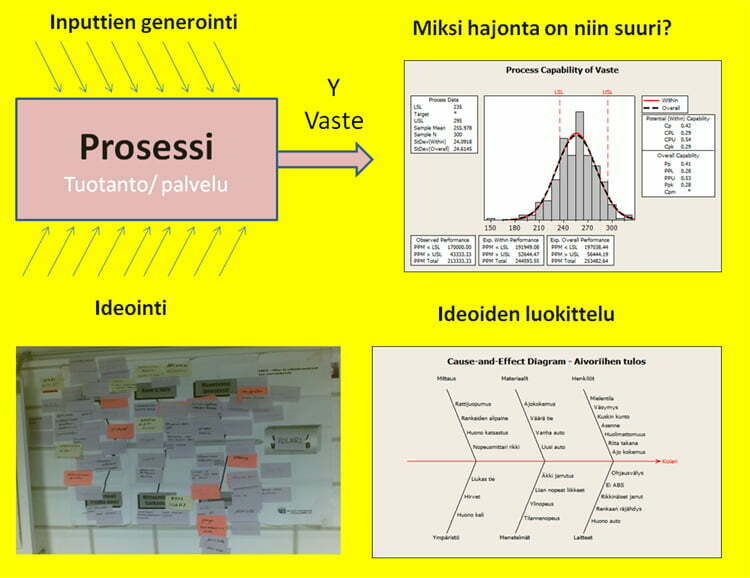
Lean Six Sigma -projekteissa mittausvaiheen aikana laajennetaan näiden muuttujien joukkoa ryhmä- ja ideointityökalujen avulla. Nyt sinulla on kymmeniä, satoja syytekijöitä. On ilmeistä, että jokaisella syyllä ei voi ole sama vaikutus ulostuloon. Toisilla on suurempi vaikutus, toisilla taas on pienempi vaikutus ja joillain ei ole vaikutusta ollenkaan. Jos sinulla on täydellinen tieto jokaisen syyn vaikutuksesta ominaisuuteen, voidaan nämä syyt laittaa järjestykseen suuremmasta pienempään.
Suurimmassa osassa tapauksia tulos muistuttaa Pareto -diagrammia. Kuvassa 4 on listattuna 21 syytä, jotka vaikuttavat ulostuloon ja kuten tavallista, vain muutama vaikuttaa suurimman osan ulostulossa havaittuun vaihteluun. Kuvassa 4 on ensimmäiset neljä tekijää (1, 2, 3 ja 4) vaikuttavat 79 %:sti. Ohjaamalla näitä neljää syytä, voidaan 79 % vaihtelusta ulostulossa selittää ja myös eliminoida.
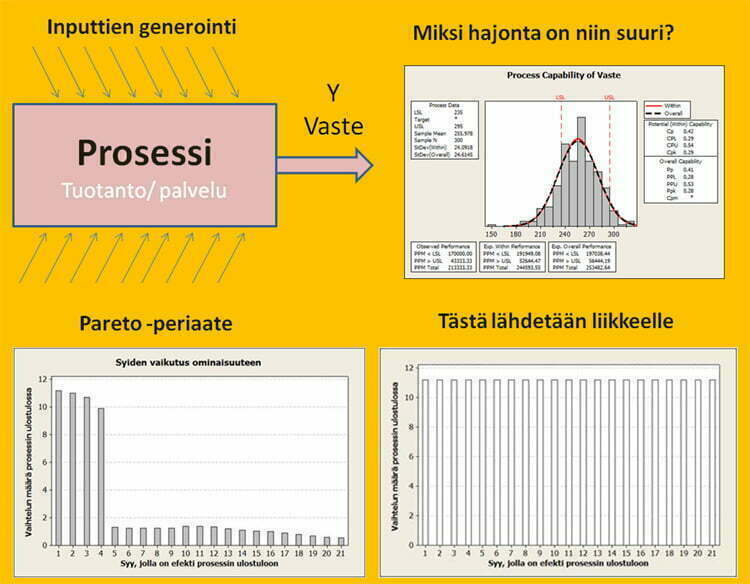
Toinen oppi Pareto-diagrammista on vähenevän tuoton periaate. Kuvassa 4 syyt 5, 6, 7, ja 8 kattavat vain 9 prosenttia koko vaihtelusta. Jos otaksutaan, että näiden lisätekijän ohjaus maksaa yhtä paljon kuin neljän ensimmäisen, silloin takaisinmaksu ohjauksesta näille on vain 1/10 neljään ensimmäiseen verrattuna. Kymmenkertainen kustannus! Neljää ensimmäistä vaihtoehtoa kutsutaankin muutamaksi kriittiseksi tekijäksi (critical few) ja muita triviaalitekijöiksi. On itsestään selvää, että kun asetetaan tuotantoprosessi, tavoitteena on tunnistaa ja ohjata kriittisiä syy-seuraustekijöiden suhteita jokaiselle avain prosessin ulostulolle. Ainoa ongelma on, että Pareto –kuvan laatiminen vaati täydellisen tiedon. Koska tämä puuttuu, mitä voidaan tehdä? Normaalisti aloitetaan siitä, että kaikki ovat yhtä tärkeitä ja pyydetään R&D:tä täyttämään tietoauko.
Valitettavasti ajan, rahan paineessa ja tehokkaiden menetelmien puuttuessa on harvinaista, että R&D tutkii kaikki listalla olevat sadat tai tuhannet syyt. Yleensä on ”teorioita” ja kokemuksen perusteella valitaan tutkittavat tekijät. Loput syyt listalla yksinkertaisesti hylätään tai unohdetaan. Kuva 5 kertoo T&K:n syytutkimuksen tulokset vasteen ominaisuuksiin.

R&D:n tutkimuksen mukaan syille 5, 1 ja 7 asetetaan ohjaus ja ne muodostavat ulostulon Y ohjaustekijät. Kuitenkin heti tuotannon alettua on ongelmia; liian paljon vaihtelua, josta syntyy liikaa viallisia. Niinpä ohjaustekijöiden joukkoon päätettiin lisätä tekijä 4. Se ei auttanut.Kun tuotannossa jäätiin yhä enemmän jälkeen tuotantosuunnitelmasta ja viallisten määrä kasvaa, aloitettiin R&D:ssä puhumaan ”taidosta”, jota tarvitaan tämän tuotteen tekemisessä. (Uskomus)sanat ”taitava”, ”guru”, ”mestari”, ”taikuus” jne tulivat käyttöön. Tarkastus ja korjaustoimia laajennettiin ja pian tuotanto-osasto oli painunut alas rutiiniin, joka on liian yleistä – ”polta paahtoleipä ja korjaa se”. Ongelma ei ollut ohjaustekijöiden setissä – niissä tekijöissä, joiden piti ohjata vaihtelua tuotevirrassa.
Ongelma ei ole kuudessa muussa tutkitussa tekijässä, joilla on vaikutus ulostuloon Y. Ongelma on niissä tekijöissä, joita T&K EI OLE tutkinut. Kuvasta 6 nähdään, että syyt 14 ja 16 ovat dominoivia syy-seuraustekijöitä. Ne ovat suurempia kuin syyt 5, 1 ja 7. Vaikka tuotanto ei ollut tietoinen syiden 14 ja 16 olemassa olosta tuotantoa jatkettiin näiden vaikutuksessa. Aina silloin tällöin, kun jompikumpi näistä tekijöistä muuttui, syntyi vastaava muutos tuoteominaisuuteen (poikkeama ja vikoja).
Jokaiselle tuoteominaisuudella on joukko dominoivia syy- ja seuraussuhteita, jotka valmistaja valitsee ohjatakseen. Näistä muodostuu ohjaustekijöiden joukko. Nämä ohjaustekijät ja niiden luonne ja mittaukset ja valvonnat esitetään Ohjaussuunnitelmassa tai toiselta nimeltä Laatusuunnitelmassa (Control plan).
Kaikki muut syy-seuraussuhteet ovat ei-ohjaamattomia ja muodostavat ei-ohjattujen joukon (uncontrolled factors). Jos tämä viimemainittu sisältää dominoivan syy-seurausefekti suhteen, tämä ei-ohjattu syy vainoaa prosessia luoden poikkeuksellista vaihtelua, ylimääräisiä kustannuksia ja yleistä kärsimystä.
Näitä dominoivia, mutta ei ohjattuja syitä, on kutsuttu erityissyiksi ”Assignable Causes” (Shewhart) tai ”Special Causes” (Deming). Jäljelle jääneitä vähemmän vaikuttavia ei-ohjattuja syitä kutsutaan satunnaissyiksi ”Common Causes” (Shewhart) tai ”Chance Cause” (Deming).
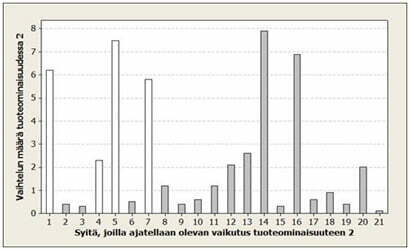
Meillä on siis ohjaustekijöitä, erityissyitä ja satunnaissyitä (Control Factors, Assignable Causes, Common Causes). Koska ohjaustekijät ovat kiinteitä, ne aiheuttavat vähän tai ei ollenkaan vaihtelua prosessin ulostuloon. Kun nämä tekijät laitetaan ohjaustekijäksi, itse asiassa poistetaan prosessivaihtelua lähteestä. Tätä kutsutaan läpimurroksi – parannuksesi. Tässä on syy, miksi hienosäätämällä ohjaustekijöitä on vain pieni tai marginaalinen vaikutus vaihteluun niin kauan kun erityissyitä on läsnä prosessissa. Toisin sanoen ammattilainen, joka säätää ohjaustekijöitä harvoin pystyy parantamaan laatua!

Et voi optimoida mitään systeemiä, jos jokin dominoiva syyefektisuhde on tunnistamatta!
Mistä teidän, onko dominoivat syy-seurausefektit tunnistettu? Vastaus on ilmiselvä, jos prosessissasi on liian paljon hallitsematonta vaihtelua, et ole valmis vielä optimointiin. Aloita stabiloimalla prosessi (laatutaulu, SPC) ja tämän jälkeen tutki syy-seuraussuhteet (Lean Six Sigma) ja etene kohti optimia. Tämä on kaikkialla mahdollista, kun opit työkalut ja tietokone orjuutetaan laskentaan.
Tehokas ja tehoton parannusstrategia
Koska aikaisemmassa esimerkissä erityissyyt 14 ja 16 muodostavat kaikki ne dominoivat tekijät, jotka eivät olleet ohjaustekijöiden joukossa, tämä ryhmä muodostaa suurimman osan ei selitettävissä olevasta vaihtelusta. Nämä tekijät ovat myös vastuussa tuotannon ylimääräisistä kustannuksista, alhaisesta laadusta, vioista ja korjauksesta. Siksi tunnistamalla erityissyyt ja tekemällä niistä osa ohjaustekijöiden ryhmää, muodostaa tehokkaan parannusstrategian (Six Sigma BB ja GB -projektit).
Yrittämällä ohjata satunnaisia syitä, saadaan parhaassakin tapauksessa, vain pieni saannon parannus. Tehoton strategia. Kun ei-ohjattujen tekijöiden joukko ei sisällä muita kuin satunnaisia syitä, prosessi on saavuttanut ekonomisen tasapainon. (Shewhart: Economic Control of Quality of Manufactured Products, 1931).
Tuotevirta on saavuttanut suurimman tasaisuuden asteen, joka on yhtäläinen ekonomisen tuotannon kanssa.

Kokeet eivät riitä!
On tärkeää huomata, että aina kun tunnistetaan dominantin syy- ja efektisuhteen ja sen jälkeen tehdään tästä ohjaustekijöiden joukon jäsenen, poistetaan vaihtelun lähde prosessista. Toisin sanoen dominoivat syyt on keksittävä T&K vaiheen aikana ja siirrettävä ohjattavien tekijöiden joukkoon, josta seuraa vaihtelun väheneminen. T&K:llä on kuitenkin rajallinen osaaminen ja rajalliset resurssit, josta seuraa, että vain osa dominoivista tekijöistä keksitään. Syy on, että aina kun päätetään tehdä koe, on olemassa enemmän tekijöitä kuin pystytään tutkimaan. Siksi on valittava ne tekijät, joita halutaan tutkia ja ne tekijät joita ei haluta tutkia. DFSS muodostaa polun, kuinka tekijät valitaan kokeeseen. Dominantit tekijät ja ei-dominantit tekijät! Onko jako oikea? Jos jako ei ole oikea, seuraa osittainen ymmärrys prosessista ja suuret laatukustannukset. Joseph M. Juranin mukaan T&K:n virheiden osuus on 80 prosenttia kaikista virheistä (tehty ennen tuotannon aloitusta suunnitteluvaiheessa) ja liikevaihdosta laskettuna 20-30 prosenttia.
Tästä seuraa, että kokeellista lähestymistapaa rajoittaa tutkijan kyky tunnistaa kaikki dominoivat syy-efektisuhteet ENNEN KOKEEN TEKEMISTÄ (suunnittelua). Se mitä kokeella (DoE) löydetään voi olla totta, mutta koko tarina voi myös olla epätäydellinen. Vaikka tarina olisi täydellinen ja ymmärrettäisiin täydellisesti mitkä tekijät ovat dominoivia tekijöitä, prosessi on aina kaikkien ei-ohjattujen tekijöiden kohteena. Kun ei ohjattujen tekijöiden joukko sisältää erityissyitä, prosessi kärsii seurauksista.
Yhteenveto
T&K-menetelmien epätäydellisyyden vuoksi tarvitaan T&K-ohjelmia täydentämään sarjan operatiivisia tutkimuksia, joilla määritetään, onko ohjaustekijöiden joukossa ”tekijän 14 ja 16” kaltaisia syitä.
Ainoa tapa selvittää tämä, on kuunnella prosessia SPC:n avulla ja oppia prosessin datasta, onko poikkeuksellista vaihtelua aiheuttanut erityissyy. Näin voidaan kehittää täydellisen tietämyksen prosessista.
Ilman tätä ymmärrystä, jatketaan toimintaa erityissyiden armoilla.
Tarvitset tekniikan, joka…
- mahdollistaa oppimaan prosessidatasta
- varoittaa, kun prosessi muuttuu
- auttaa tunnistamaan muutosten syyt
- mahdollistaa sinun operoida prosessia ennustettavasti ja tavoitteessa
Aikaisemmat tähän aiheeseen liittyvät artikkelit ovat:
I. osa: käsittelee datan laatua ja laatuteknologian rooli datan laadun parantamisessa, 27.1.2009
II. osa: käsittelee datan analyysiä; signaali vs. kohina, 13.2.2009
III. osa: käsittelee datan keräystä ja signaalityyppejä, 11.3.2009
Tilaa uutiskirje
Liity postituslistalle ja saat uusimmat artikkelit suoraan sähköpostiisi.
Tämä lomake on suojattu Google reCAPTCHA:lla. Lue tietosuojaseloste ja käyttöehdot.
Liittymällä postituslistalle hyväksyt Quality Knowhow Karjalainen Oy:n tietosuojaselosteen ja Quality Knowhow Karjalainen Oy voi lähettää sinulle ajankohtaisia artikkeleita, videoita sekä tietoa ja tarjouksia kursseista, kirjoista sekä ohjelmistoista.
Tämä lomake on suojattu Google reCAPTCHA:lla. Lue tietosuojaseloste ja käyttöehdot.